1 前言
水是生命的源泉,地球與其它星球之區(qū)別就在于地球上有水,依靠水的支持由低級(jí)生物進(jìn)化到有高度文明的人類。人類創(chuàng)造了文明,進(jìn)而人類享受文明創(chuàng)造的財(cái)富和美好環(huán)境,但是現(xiàn)代人過度的向地球索取,奢侈地用水和污染水,使水資源承載巨大的壓力。水資源逐漸枯竭,最終人類會(huì)被自己創(chuàng)造的文明毀滅。氮肥工業(yè)為重點(diǎn)污染行業(yè)之一,是化工行業(yè)中主要排污大戶,其廢水排放量占全國(guó)廢水排放量的10%左右,治理勢(shì)在必行,這就是推廣應(yīng)用氮肥生產(chǎn)污水零排放技術(shù)從而實(shí)現(xiàn)氮肥生產(chǎn)污水零排放的意義所在。
2 氮肥生產(chǎn)環(huán)境現(xiàn)狀
我國(guó)氮肥工業(yè)2006年生產(chǎn)合成氨4937.9萬(wàn)噸,氮肥3440萬(wàn)噸(折純N),其中尿素4578.6萬(wàn)噸(實(shí)物量),氮肥產(chǎn)量和尿素產(chǎn)量均居世界第一位,在我國(guó)農(nóng)業(yè)發(fā)展中發(fā)揮了重要作用。我國(guó)煤制合成氨占合成氨總產(chǎn)量的76%,這些裝置的中間產(chǎn)品是合成氨,以氨加工碳銨、尿素,也有部分聯(lián)產(chǎn)甲醇。
以年產(chǎn)10萬(wàn)噸合成氨、2萬(wàn)噸甲醇的氮肥生產(chǎn)裝置為例,其主要產(chǎn)品為尿素、碳銨、甲醇,工藝流程及主要污染源情況如圖一:
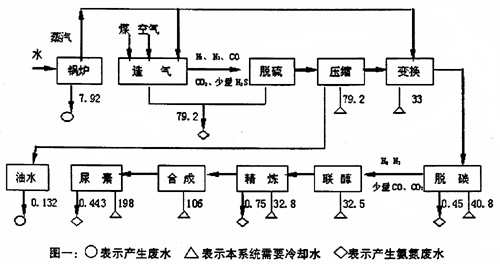
由圖一看出,每生產(chǎn)1噸氨,需要冷卻水522.3噸,產(chǎn)生氨氮廢水80.84噸,其它廢水8.05噸。廢水來自造氣的洗滌塔和沖渣,含固量高、溫度高、成份復(fù)雜;鍋爐電站的除塵和沖渣;脫硫液稀氨水;碳化稀氨水;尿素廢液污水;脫鹽水工段樹脂再生的廢水;銅洗精煉稀氨水及含銅液廢水;甲醇精餾殘液;冷卻水排放等。
3 治理技術(shù)方案
做好氮肥生產(chǎn)裝置的廢水治理,實(shí)現(xiàn)污水零排放,必須從源頭抓起,首先要節(jié)約用水,冷卻水循環(huán)使用,提高循環(huán)倍數(shù);采用清潔生產(chǎn)工藝,從源頭消除污染源,不產(chǎn)生污水;用先進(jìn)方法治理污水,因地制宜做到零排放。
3.1 建立三水閉路循環(huán),在循環(huán)中對(duì)污水中氨、氮、氰進(jìn)行處理。
3.1.1造氣脫硫污水閉路循環(huán)處理系統(tǒng)
造氣脫硫污水是洗滌冷卻煤氣的洗滌水和,氨水脫硫排出的脫硫氨水,其主要污染物是煤粉、氰、氨氮等。
減少污水量,選用先進(jìn)造氣工藝,提高蒸汽分解率達(dá)到44%以上;回收煤氣、吹風(fēng)氣顯熱和潛熱,副產(chǎn)蒸汽,減少冷凝蒸汽和冷卻煤氣的冷卻水量;洗滌水采用平流沉淀、微渦流澄清,使懸浮物降至40mg/l~50mg/l;加入磷酸鎂使之與氨進(jìn)行反應(yīng)生成磷酸銨鎂沉淀,污泥處理后做肥料使用;采用微電解法使氰化物、硫化物與鐵屑進(jìn)行電化反應(yīng),生成不溶物,沉淀除去。
脫硫工藝必須淘汰落后的氨水脫硫,采用栲膠脫硫,消除一個(gè)氨氮污染源;采用戈?duì)柲ひ后w過濾器及程序控制系統(tǒng),進(jìn)行硫泡沫處理;采用連續(xù)熔硫技術(shù),收集硫磺產(chǎn)品,達(dá)到懸浮液硫含量≤5ppm,液體循環(huán)使用。
3.1.2建立鍋爐污水循環(huán)系統(tǒng)
鍋爐污水是水洗鍋爐煙氣形成的,煙氣經(jīng)過脫硫處理后,經(jīng)麻石水膜除塵器噴水除塵,再經(jīng)混凝處理,兩級(jí)沉淀,一級(jí)過濾,形成閉路循環(huán)。
兩個(gè)閉路循環(huán)系統(tǒng)在循環(huán)過程中,因蒸發(fā)需補(bǔ)充水以維持平衡。兩個(gè)閉路循環(huán)的補(bǔ)充水不需一次水,利用冷卻水循環(huán)系統(tǒng)的部分循環(huán)水補(bǔ)充到造氣脫硫污水循環(huán)系統(tǒng),造氣脫硫污水系統(tǒng)的循環(huán)水經(jīng)過回收油后補(bǔ)充至鍋爐污水循環(huán)系統(tǒng)。
3.1.3建立冷卻水閉路循環(huán)系統(tǒng)
氮肥生產(chǎn)的反應(yīng)過程中必須將反應(yīng)氣體加熱到一定溫度,在反應(yīng)過程中產(chǎn)生大量的熱量,如變換反應(yīng)、甲醇合成反應(yīng)、氨合成反應(yīng),都有大量反應(yīng)熱放出形成高溫氣體,而在氣體凈化、精制、分離過程中又要將高溫氣體(包括壓縮氣體產(chǎn)生的高溫氣體)冷卻,因此要提高熱回收利用率和減少冷卻水用量。
冷卻水的特點(diǎn)是水量大,如果冷卻水直流排放,噸氨需要522噸水,因此要單獨(dú)建立閉路循環(huán)系統(tǒng)。為了減少循環(huán)水量,首先必須革新工藝技術(shù),多回收熱氣體的熱量以降低工藝氣體的溫度,一般都應(yīng)降至60℃~70℃,再用冷卻水間接冷卻,采用這一措施,可使冷卻水減少30%左右。為了保護(hù)水質(zhì)并提高冷卻效果,采用高效換熱冷卻設(shè)備;對(duì)循環(huán)水進(jìn)行阻垢緩蝕、殺菌、滅藻處理,如采用物理法離子棒水處理器,可以達(dá)到上述目的或加入無(wú)磷降解水質(zhì)穩(wěn)定劑。
循環(huán)冷卻水在循環(huán)過程中,部分蒸發(fā),需要補(bǔ)充水,最好采用軟水,提高循環(huán)倍數(shù),減少一次水用量。
3.2 采用先進(jìn)生產(chǎn)工藝,消除污染源
治污必須從源頭消除污染源,即盡量減少水的污染。在氮肥生產(chǎn)中除了上述的造氣、鍋爐、脫硫污染源外,還有兩大污染源,一是銅洗精制原料氣,它有大量稀氨水排放和銅氨液的跑冒滴漏;另一個(gè)污染源是尿素工藝?yán)淠海写罅康哪蛩睾桶薄?/DIV>
3.2.1用醇烴化精制工藝取代銅洗精制工藝。
醇烴化工藝,即用甲醇化、烴化將原料中少量的CO、CO2先轉(zhuǎn)化成甲醇,剩余的CO、CO2轉(zhuǎn)化低碳烴類,使原料氣中CO+CO2≤10ppm。
醇烴化工藝獲得了國(guó)家科技進(jìn)步二等獎(jiǎng),是國(guó)家重點(diǎn)環(huán)境保護(hù)實(shí)用技術(shù)A類項(xiàng)目。
醇烴化的反應(yīng)式如下:
醇化:CO+2H2=CH3OH
CO2+3H2=CH3OH+H2O
烴化:(2n+1)H2+nCO→4CnH(2n+2)+nH2O
2nH2+nCO→CnH2n+nH2O
2nH2+nCO→CnH(2n+2)O+(n-1)H2O
(3n+1)H2+nCO2→CnH(2n+2)+2nH2O
醇烴化工藝流程圖如圖二:
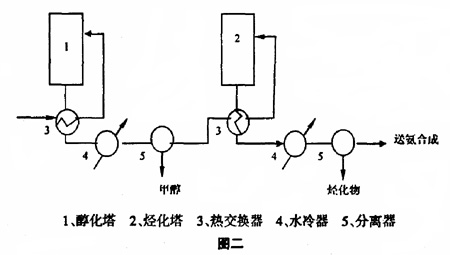
原料氣預(yù)熱后進(jìn)醇化塔反應(yīng),反應(yīng)后熱氣經(jīng)冷卻換熱、水冷,甲醇冷凝為液體分離,分離后氣體含有~0.1%的CO、CO2,經(jīng)預(yù)熱,進(jìn)行烴化反應(yīng),反應(yīng)后氣體經(jīng)換熱冷卻冷凝,分離出烴化物,出系統(tǒng)氣體中CO+CO2<10ppm,送氨合成。
由圖二可以看出,醇烴化工藝有甲醇和烴化物生成,這兩種都是可利用的化工原料和燃料,能產(chǎn)生顯著的經(jīng)濟(jì)效益。
3.2.2 尿素工藝?yán)淠荷疃人?/DIV>
尿素生產(chǎn)中,按反應(yīng)式2個(gè)NH3與—個(gè)CO2反應(yīng)生成—個(gè)尿素(NH2)2CO和—個(gè)水,每生產(chǎn)一噸尿素理論生成300kg水,加上蒸汽及沖洗水,約為350kg~400kg,形成含有大量NH3和(NH2)2CO的冷凝液。國(guó)內(nèi)許多尿素生產(chǎn)裝置只經(jīng)過簡(jiǎn)單的解吸,其排出液含NH3量仍達(dá)到6000ppm~10000ppm,含尿素1.0%~2.0%,排放后嚴(yán)重污染環(huán)境。
用解吸深度水解法,經(jīng)水解后,廢液即成為精制水,含氨≤5ppm、尿素≤5ppm,可做鍋爐給水。解吸深度水解法有中壓法和低壓法,圖三為低壓法工藝流程:
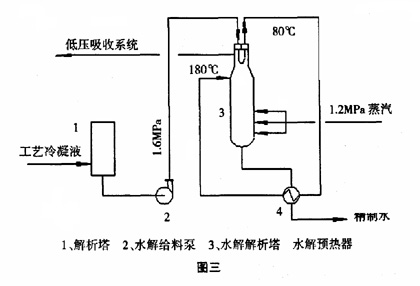
該法包括一個(gè)解吸塔(可用原塔)、一個(gè)水解解吸塔(操作壓力為1.05~1.15MPa,溫度170~190℃)和一臺(tái)水解給料泵,處理后廢液中氨和尿素分別為3~5ppm,做為精制鍋爐給水。
3.3 終端處理
3.3.1 圍堰和事故池
通過源頭治理并實(shí)現(xiàn)了兩個(gè)污水閉路循環(huán)和冷卻水閉路循環(huán)之后,尚有一些分散的小股廢水排放,如隔油后油水分離器排水、水封排水、泄漏水、水處理系統(tǒng)排污水、鍋爐排污水、地面沖洗水、生活洗滌水、檢修和事故狀態(tài)下排出的廢液、廢水,以及兩個(gè)污水循環(huán)系統(tǒng)排出水,為此,根據(jù)工段的特點(diǎn)設(shè)置圍堰和事故池,清濁分流,分級(jí)利用,雨污分流,雨水直接外排;污水與初期雨水均收集于事故池中,集中進(jìn)行終端處理。
3.3.2氣升式環(huán)流生物處理技術(shù)
氣升式環(huán)流反應(yīng)器是一種單位體積COD、氨氮負(fù)荷大,操作彈性大,抗沖擊能力強(qiáng)、操作費(fèi)用低的一種有效的生化法處理反應(yīng)器,其工藝流程圖如圖四:
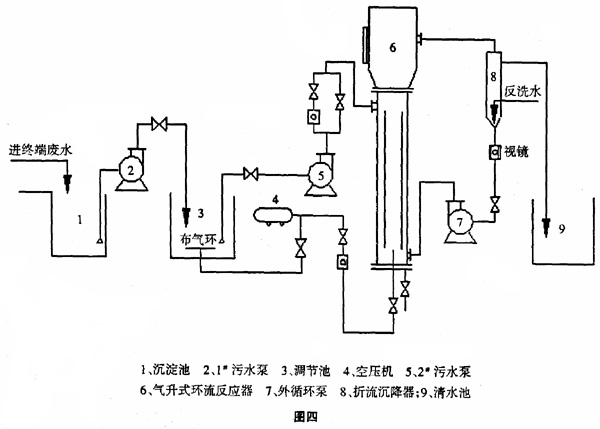
進(jìn)入終端的廢水由1#泵抽送到調(diào)節(jié)池,在調(diào)節(jié)池下布設(shè)一些曝氣環(huán),經(jīng)過初步曝氣后的廢水由2#泵送入氣升式環(huán)流反應(yīng)器的上部,反應(yīng)器的下部由空壓機(jī)送入空氣進(jìn)行曝氣,處理后的廢水從上部自流進(jìn)入折流沉降器中,沉降器中的清水部分溢流進(jìn)入清水池,沉降器下部污泥用泵重新打入環(huán)流反應(yīng)器中。
終端廢水采用氣升式環(huán)流反應(yīng)器生物法處理,處理后的水質(zhì)能達(dá)到《生活雜用水水質(zhì)標(biāo)準(zhǔn)CJ/T48-1999》中城市綠化的水質(zhì)要求(該標(biāo)準(zhǔn)的水質(zhì)要求嚴(yán)于《合成氨工業(yè)水污染物排放標(biāo)準(zhǔn)GB13458—2001》中的一級(jí)排放標(biāo)準(zhǔn),同時(shí)也嚴(yán)于《污水綜合排放標(biāo)準(zhǔn)GB8978-1996)中的一級(jí)標(biāo)準(zhǔn))。
3.4 水平衡
經(jīng)過上述的處理,氮肥生產(chǎn)中補(bǔ)充新鮮水大為減少,噸氨廢水排放量控制在2t以下,基本不向外排廢水。按年產(chǎn)10萬(wàn)噸合成氨、2萬(wàn)噸甲醇的裝置進(jìn)行水平衡,補(bǔ)充新鮮水為172.1t/h,即噸氨補(bǔ)充新鮮水為11.36噸,其中循環(huán)過程蒸發(fā)水為101.6噸/h,生產(chǎn)過程化學(xué)反應(yīng)消耗水為48.2t/h,沖渣帶走水4.4t/h,經(jīng)終端處理后的排放水(不含污染物)17.9t/h(1.18t/tNH3)可再生回用,基本上實(shí)現(xiàn)氮肥生產(chǎn)污水零排放。
4 應(yīng)用情況
2003年,在中國(guó)氮肥工業(yè)協(xié)會(huì)的組織下,我公司組織技術(shù)人員深入企業(yè)進(jìn)行了大量的調(diào)查研究和可行性論證,充分利用公司的技術(shù)優(yōu)勢(shì),僅用4個(gè)月時(shí)間完成了技術(shù)先進(jìn)、成熟、可靠的《氮肥生產(chǎn)污水零排放綜合治理環(huán)保工程通用設(shè)計(jì)》的編制工作,同年年底該套通用設(shè)計(jì)通過了國(guó)家環(huán)保總局領(lǐng)導(dǎo)和專家的審查,得到了高度評(píng)價(jià),建議在氮肥行業(yè)大力推廣應(yīng)用。
2004年至2006年納入中央環(huán)境保護(hù)專項(xiàng)資金支持的29家氮肥企業(yè),有25家采用了通用設(shè)計(jì),2005年納入國(guó)家發(fā)改委國(guó)債支持的淮河流域項(xiàng)目的22家氮肥企業(yè)全部采用了通用設(shè)計(jì)。47家氮肥企業(yè)通過實(shí)施污水零排放項(xiàng)目,取得了巨大的環(huán)保效益,每年減少一次水用量13065萬(wàn)噸,減少?gòu)U水排放11437萬(wàn)噸,其中減排COD1.3萬(wàn)噸、SS9900噸、氨氮1.3萬(wàn)噸、氰化物118噸、硫化物158噸、石油類698噸、揮發(fā)酚34噸。
至今為止,我公司已為近80家氮肥企業(yè)提供了環(huán)保技術(shù)咨詢,將通用設(shè)計(jì)與企業(yè)的具體情況相結(jié)合,堅(jiān)持通用化的同時(shí)突出個(gè)性化,一廠一設(shè)計(jì),廠廠各不同。今年召開的全國(guó)氮肥工業(yè)環(huán)保工作經(jīng)驗(yàn)交流會(huì)參觀的河南心連心化肥有限公司和石家莊正元化肥有限公司兩個(gè)現(xiàn)場(chǎng),均按通用設(shè)計(jì)實(shí)施,得到了環(huán)?偩趾透骷(jí)政府的認(rèn)可,是實(shí)施污水零排放技術(shù)的示范。下面介紹幾家企業(yè)在實(shí)施通用設(shè)計(jì)中的具體的做法。
實(shí)例一:河南心連心化工有限公司
①采用醇烴化精制工藝,砍掉傳統(tǒng)的銅洗工藝
原合成氨生產(chǎn)系統(tǒng)原料其精致采用的是傳統(tǒng)銅洗工藝,在銅洗再生過程中,產(chǎn)生解析廢氣,需用軟水吸收產(chǎn)生稀氨水(年約3萬(wàn)噸),利用價(jià)值低并污染環(huán)境。2003年大膽采用湖南安淳公司技術(shù),利用原Ф1000合成系統(tǒng)的主要設(shè)備,成功改造成為“醇烴化”工藝,取代了銅洗,根本解決了合成氨原料氣凈化精制系統(tǒng)NH3-N污染問題。年削減NH3-N總量65噸,副產(chǎn)甲醇,取得了經(jīng)濟(jì)與環(huán)境雙贏的好成效。
②改造脫鹽水工段,提高出水率,減少排放
原鍋爐給水采用的是離子交換工藝,需要鹽酸和燒堿對(duì)樹脂進(jìn)行再生,再生時(shí)排出酸、堿廢液(約10m3/h)腐蝕性強(qiáng),必須加堿、酸中和,中和后廢液COD高達(dá)650mg/l,直接排放對(duì)水體污染嚴(yán)重。采用反滲透膜分離技術(shù)取代原有的離子交換工藝,該技術(shù)屬無(wú)相變物理方法制取純水,不用化學(xué)藥劑和酸堿再生處理,所排濃水沒有污染,可直接排放。該項(xiàng)改造每年可減少COD排放量約25噸,環(huán)境效益明顯。
③完善造氣廢水處理,優(yōu)化造氣工藝,實(shí)現(xiàn)零排放
在穩(wěn)定造氣工藝的基礎(chǔ)上,把微渦流塔板澄清技術(shù)應(yīng)用干造氣污水治理,提高水的重復(fù)利用率(99%以上)。與此同時(shí)把好入爐原料關(guān),逐步進(jìn)行爐體結(jié)構(gòu)技術(shù)改造,穩(wěn)定優(yōu)化工況條件,提高蒸汽分解率,減少冷凝液富余帶入造氣循環(huán)水系統(tǒng),攻克了造氣污水閉路困難的技術(shù)難題。
④采用中壓深度水解解吸新工藝,回收尿素、氨,實(shí)現(xiàn)氨氮零排放
由于尿素解吸液超標(biāo)排放造成了排污水中NH3—N嚴(yán)重超標(biāo),為解決這一問題,結(jié)合本工司的工藝現(xiàn)狀,對(duì)解吸液中的尿素、NH3-N采用深度水解、解吸技術(shù),投入運(yùn)行后,尿素解吸液中尿素、NH3—N的含量由改造前的1%、0.07%分別降至5ppm、15ppm以下,同時(shí)年回收尿素1000余噸,價(jià)值15萬(wàn)元,取得了理想的經(jīng)濟(jì)效益和環(huán)境效益。
⑤處理甲醇精餾殘液
甲醇生產(chǎn)中精餾塔底部排放的殘液,每生產(chǎn)1噸精醇產(chǎn)生300~500kg,其中COD含量高達(dá)10000mg/l,若直接排放,對(duì)水體污染嚴(yán)重。因公司污水終端處理采用生化技術(shù),C/N比失調(diào),影響處理效果,降甲醇?xì)堃核椭两K端處理系統(tǒng),既穩(wěn)定了微生物的生存條件,化害為利,又保證了處理效果。
⑥建立事故排放池,建立廢水清濁分流、分級(jí)使用網(wǎng)絡(luò)
壓縮各段排油水(3m3/h、COD3000mg/l、NH3-N620mg/l)經(jīng)隔油分離后直接送電站鍋爐煤場(chǎng)噴灑煤灰使用;各主要工段與污水終端處理站建立污染事故排放池,正常高濃度工藝?yán)淠号c事故性排放全部排至崗位事故池,然后由管道逐漸送終端處理或作為造氣循環(huán)冷卻水補(bǔ)充水;生產(chǎn)區(qū)域所有地溝僅為清水排放和雨季使用;停車檢修、沖塔清洗、清池置換的大量排污直接排入污水終端處的事故池,緩慢定量連續(xù)處理。
實(shí)例二:石家莊正元化肥有限公司
①改造造氣廢水處理系統(tǒng),實(shí)現(xiàn)閉路循環(huán)
造氣循環(huán)水分為兩級(jí)循環(huán),洗氣塔分為兩段,下段為除塵段,上段為降溫段,除塵段由一級(jí)循環(huán)水供給,主要洗去半水煤氣中的灰塵,控制下段洗氣塔半水煤氣出口溫度,除塵后污水經(jīng)沉淀池沉淀后,入熱水池,由熱水泵送入除塵段頂部;降溫段由二級(jí)循環(huán)水供給,降溫后熱水入熱水池,由熱水泵送入涼水塔降溫,再由涼水泵加壓供降溫段使用。本技術(shù)的關(guān)鍵是半水煤氣中的飽和水在除塵段不冷凝,同時(shí)除塵水部分蒸發(fā),該部分水在降溫段以蒸汽冷凝液的形式隨降溫水冷凝,十二級(jí)降溫水不斷漲水,自其中取走富余水(水質(zhì)接近蒸汽冷凝液)入終端處理,保證了造氣循環(huán)水虧水,處于水平衡狀態(tài)。除塵段補(bǔ)水由脫硫循環(huán)水補(bǔ)入,保證了脫硫循環(huán)水的置換,處于清水狀態(tài),同時(shí)由于控制了洗氣塔除塵段溫度,除塵段水隨半水煤氣帶入降溫段,將水取走,保證了其他工段的污水補(bǔ)入。
②清濁分流、分級(jí)使用
造氣工段油冷卻器、羅茨風(fēng)機(jī)油冷、甲醇循環(huán)機(jī)油冷卻器水為一次水,冷卻后的水進(jìn)入一次水池進(jìn)行回收利用。
變換工段熱水塔排放水、冷卻器排放水,排入甲醇循環(huán)水作為補(bǔ)水。
甲醇水洗塔排放水、油進(jìn)行回收,水排入鍋爐循環(huán)水作為補(bǔ)水。
甲醇、合成、尿素、精餾、脫碳循環(huán)水均設(shè)有循環(huán)水旁濾器進(jìn)行過濾,其反洗水為減少二次污染,均通過封閉管道直接排入終端池進(jìn)行終端處理。
提H2崗位濃氨水經(jīng)蒸氨后的殘液(含極微量氨),帶壓送飽和熱水塔作為補(bǔ)水,即得到了充分應(yīng)用,由調(diào)節(jié)了飽和熱水的PH值,有利于飽和塔的防腐。
③尿素解吸廢液增濃回收
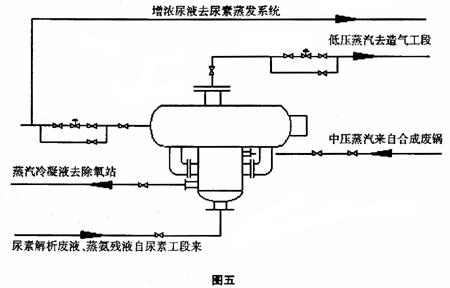
如圖五所示的增濃裝置,來自尿素工段的解吸廢液,送入解吸廢液增濃裝置,利用合成廢鍋生產(chǎn)的0.5~0.8Mpa低壓蒸汽進(jìn)行加熱增濃,產(chǎn)生的低壓蒸汽通過壓力調(diào)節(jié)閥送造氣系統(tǒng)制取半水煤氣,蒸汽冷凝液送除氧站回收利用;解吸廢液經(jīng)加熱蒸發(fā)后,濃度不斷增加,尿素含量達(dá)到20%左右,送尿素蒸發(fā)系統(tǒng)進(jìn)行回收尿素。通過本裝置的回收,一方面回收低壓蒸汽,同時(shí)回收了尿素,閉路循環(huán),不排放,實(shí)現(xiàn)了零排放。
④終端處理
經(jīng)過前端的源頭治理和水的梯級(jí)利用,到達(dá)終端的只有冷卻水循環(huán)系統(tǒng)的置換水,由于循環(huán)水系統(tǒng)補(bǔ)入的是反滲透脫鹽水,大大提高了循環(huán)倍數(shù),置換水量少,終端也只用簡(jiǎn)單的處理。各循環(huán)水經(jīng)旁濾器反洗水進(jìn)入終端池,經(jīng)集水池穩(wěn)質(zhì)后加藥絮凝沉降進(jìn)入清水池,由清水泵經(jīng)過濾器送入合成、甲醇系統(tǒng)作為循環(huán)水補(bǔ)水。若鍋爐造氣水虧水可取部分甲醇循環(huán)水作為鍋爐循環(huán)水補(bǔ)水,可以降低整套循環(huán)水鈣鎂離子、氯離子。
實(shí)例三:張家港市華源化工有限公司
該公司的搬遷技改項(xiàng)目15萬(wàn)噸/年合成氨、50萬(wàn)噸/年復(fù)合肥、15萬(wàn)噸/年尿素均為新建,區(qū)內(nèi)還有熱電工程。該項(xiàng)目在具備“三同時(shí)”的條件下于2005年10月投入運(yùn)行,效果顯著,在環(huán)保方面突出的做法是:
①選用先進(jìn)、可靠的清潔生產(chǎn)工藝技術(shù),源頭把關(guān),杜絕污染
合成氨流程:以白煤、水蒸氣為原料,采用固定床造氣、半水煤氣栲膠脫硫、經(jīng)中低低變換、DDS脫硫、MEDA脫碳、醇烴化精制,最后進(jìn)入氨合成;尿素生產(chǎn)采用二氧化碳汽提工藝,尿素工藝廢水采用深度水解,回收氨,處理后水中氨和尿素的濃度為10mg/l,不含其他雜質(zhì),可作為軟水回用于鍋爐。
②清濁分流、雨污分流、一水多用
廠區(qū)內(nèi)規(guī)劃建設(shè)了排水管網(wǎng),清水排入護(hù)漕港再入長(zhǎng)江;建立了污水終端處理系統(tǒng)(污水處理站),污水排放口安裝了監(jiān)測(cè)儀器。
設(shè)置專用的一次水凈水站,對(duì)一次水進(jìn)行凈化處理,凈水站的反沖洗水,主要污染物位SS和COD,送入污水處理站調(diào)節(jié)池與其它廢水混合,一并處理。
每個(gè)生產(chǎn)單元設(shè)置不同類型、規(guī)格的圍堰和事故池,排污水、沖洗水、初期雨水等收集后統(tǒng)一送污水處理站調(diào)節(jié)池。
③造氣廢水循環(huán)處理
造氣循環(huán)水系統(tǒng)除設(shè)立常規(guī)的平流沉淀池和斜管沉淀池外,還設(shè)置了橫流式混流生物塔,處理氰化物、硫化物、揮發(fā)酚等有毒有害物質(zhì),該生物塔式處理造氣廢水的新技術(shù),處理效果好。
5 結(jié)語(yǔ)
氮肥生產(chǎn)污水零排放技術(shù)已在氮肥行業(yè)取得了成功應(yīng)用,其環(huán)境保護(hù)和節(jié)能降耗效果顯著。國(guó)內(nèi)現(xiàn)有的氮肥企業(yè)生產(chǎn)裝置規(guī)模、技術(shù)、管理水平參差不齊,各企業(yè)應(yīng)根據(jù)實(shí)際情況,有的放矢地選擇切實(shí)可行的工藝技術(shù)進(jìn)行環(huán)境治理,搞好清潔生產(chǎn),走循環(huán)經(jīng)濟(jì)之路,實(shí)現(xiàn)企業(yè)可持續(xù)發(fā)展。作為設(shè)計(jì)單位和技術(shù)擁有單位,我們將一如既往的為氮肥行業(yè)的進(jìn)步和企業(yè)的發(fā)展而提供優(yōu)質(zhì)服務(wù)。

元豐資訊:
氮肥與甲醇技術(shù)網(wǎng)
尿素網(wǎng)
造氣網(wǎng)
二甲醚網(wǎng)
尿素世界網(wǎng) (英文版)
產(chǎn)品技術(shù)庫(kù)
VIP商務(wù)俱樂部
化工論壇
QQ群大聯(lián)盟
| 會(huì)員登錄 |
網(wǎng)站地圖 |
意見反饋 |
關(guān)于我們 |
聯(lián)系我們 |
網(wǎng)站指南 |
法律申明 |
保護(hù)隱私權(quán) |
致作者 |
Copyright © 2008-2010 中國(guó)氮肥與甲醇技術(shù)網(wǎng) 版權(quán)所有 蜀ICP備05031754號(hào) E-mail:yf116@vip.163.com
地址:成都市青白江區(qū)怡湖芳鄰18棟8號(hào) 電話:028-83667786,83667576,89309098 傳真:028-83667578