湖北省化學(xué)研究院于1984年開(kāi)始研究球形耐硫變換催化劑,即B302Q。該催化劑首先應(yīng)用于中小型化肥廠的中串低工藝,于1988年完成了國(guó)內(nèi)第1個(gè)中型廠的中串低工藝改造。在下一步是研究串2個(gè)低變的中低低工藝還是3個(gè)低變的全低變工藝的問(wèn)題上,經(jīng)比較后認(rèn)為中低低本質(zhì)上仍然是中串低工藝,故將下一個(gè)研究目標(biāo)確定為全低變工藝。該項(xiàng)研究于1989年開(kāi)始工業(yè)試驗(yàn),經(jīng)過(guò)18年的開(kāi)發(fā)和改進(jìn),全低變工藝技術(shù)逐步從不成熟走向完善,目前已成功地應(yīng)用于國(guó)內(nèi)外200多套大小不同的裝置中,為化肥等行業(yè)的節(jié)能降耗及甲醇工業(yè)的發(fā)展做出了積極的貢獻(xiàn)。筆者作為該項(xiàng)技術(shù)的發(fā)明人之一,擬在全低變工藝成功實(shí)施200例之際,對(duì)該工藝改造的理論基礎(chǔ)和技術(shù)優(yōu)勢(shì)進(jìn)行總結(jié),以供業(yè)界決策者和技術(shù)人員參考。
1 全低變工藝研發(fā)過(guò)程
全低變工藝的研究開(kāi)發(fā)過(guò)程大致可分為以下4個(gè)階段。
(1)第1階段為理論研究、保護(hù)劑研究以及工業(yè)實(shí)驗(yàn)階段,時(shí)間為1989年,在湖北鄖縣化肥廠進(jìn)行了第1次工業(yè)試驗(yàn),取得階段性成果。
(2)第2階段為工業(yè)應(yīng)用初級(jí)階段,時(shí)間為1990~1991年,在湖北利川市化肥廠進(jìn)行第1次工業(yè)應(yīng)用,同年又在湖北的武昌、蘄春,江蘇淮陰、盱眙、金湖等11個(gè)化肥廠進(jìn)行了工業(yè)應(yīng)用。上述各廠均是在原中串低或中變流程基礎(chǔ)上進(jìn)行簡(jiǎn)單改造完成的。雖然通過(guò)了技術(shù)鑒定,但當(dāng)時(shí)該技術(shù)仍存在3個(gè)問(wèn)題:①設(shè)備不配套;②工藝不完善;③催化劑存在失活問(wèn)題。
(3)第3階段為技術(shù)完成階段,時(shí)間為1992年,在江蘇丹陽(yáng)化肥廠實(shí)施第1套標(biāo)準(zhǔn)設(shè)計(jì)的全低變工藝。該廠有1爐催化劑連續(xù)使用了12年,噸氨耗蒸汽≤250kg。江蘇丹陽(yáng)化肥廠全低變工藝的成功實(shí)施,標(biāo)志著全低變技術(shù)從工藝設(shè)計(jì)、設(shè)備配套到催化劑的失活等問(wèn)題全部得到解決,同時(shí)還證明全低變技術(shù)從不成熟走向了完善。
(4)第4階段為技術(shù)推廣階段,時(shí)間為1993年迄今,全低變技術(shù)開(kāi)始大范圍地在中小型氮肥企業(yè)推廣運(yùn)用。近5年來(lái)隨著甲醇行業(yè)的發(fā)展,全低變技術(shù)在這一領(lǐng)域得到了普遍采用。該技術(shù)在大量的工藝實(shí)施中,技術(shù)本身也得到了不斷完善,如全部取消調(diào)溫水加熱器的噴水增濕技術(shù),無(wú)飽和塔流程,部分變換串中溫水解技術(shù)等。這一階段存在主要問(wèn)題有:①不具備開(kāi)發(fā)全低變技術(shù)的催化劑生產(chǎn)單位也開(kāi)始推廣全低變工藝。據(jù)不完全統(tǒng)計(jì),先后有5個(gè)生產(chǎn)耐硫變換催化劑的單位在10多家中小型企業(yè)進(jìn)行全低變工藝的工業(yè)應(yīng)用實(shí)施工作,均以失敗告終;②在這些失敗的案例發(fā)生以后,少數(shù)技術(shù)人員在不明白失敗真實(shí)原因情況下對(duì)全低變技術(shù)作出了一些不科學(xué)的評(píng)價(jià),在行業(yè)內(nèi)造成不良影響;③有些企業(yè)對(duì)全低變工藝的一些技術(shù)細(xì)節(jié)重視不夠,操作控制不嚴(yán)也影響了全低變技術(shù)的經(jīng)濟(jì)效益。
2 鐵鉻中變催化劑的不足之處
近20年來(lái),在變換催化劑和變換技術(shù)的工業(yè)實(shí)踐中經(jīng)常有企業(yè)反映Fe-Cr系中變催化劑的一些問(wèn)題,最普遍的問(wèn)題是相當(dāng)多的中小型化肥廠每年大修時(shí)都對(duì)中變催化劑進(jìn)行1/3~1/2不等的更換處理,不僅勞動(dòng)強(qiáng)度大,而且增加了購(gòu)買催化劑的費(fèi)用。經(jīng)調(diào)查研究發(fā)現(xiàn),無(wú)論是中串低工藝還是中低低工藝,F(xiàn)e-Cr系催化劑都會(huì)表現(xiàn)出以下4個(gè)突出的缺點(diǎn):①活性溫度高,導(dǎo)致熱損大,蒸汽消耗高,阻力相對(duì)也大;②相對(duì)于耐硫低變催化劑而言,易粉化,易被硫等毒物中毒,使用壽命短;③在相同的生產(chǎn)能力前提下,使用Fe-Cr催化劑需要較大型的設(shè)備,因此一次性投資和維修費(fèi)用均高于全低變工藝;④費(fèi)托反應(yīng)問(wèn)題。筆者針對(duì)這4個(gè)問(wèn)題產(chǎn)生的原因分析如下。
2.1 Fe-Cr催化劑打片成形
目前工業(yè)中使用的Fe-Cr催化劑均是采用物理方法打片成形,一直存在著“活性較好,強(qiáng)度較差”的問(wèn)題。雖然催化劑牌號(hào)不斷涌現(xiàn),但這一“老大難”問(wèn)題至今未能得到徹底解決,對(duì)催化劑的粉化留下了隱患。
2.2 費(fèi)托副反應(yīng)與硫的影響
當(dāng)CO/CO2摩爾比在1.6以上,進(jìn)口汽氣比小于0.6時(shí),副產(chǎn)物的生成量可達(dá)到百萬(wàn)分之?dāng)?shù)百(見(jiàn)表1)。雖然在0.8 MPa條件下情況會(huì)有所改善,但也要引起足夠注意。國(guó)產(chǎn)中變催化劑的進(jìn)口汽氣比一般不宜小于0.4。
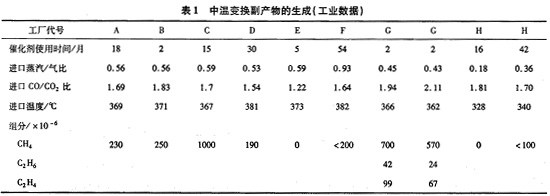
這個(gè)問(wèn)題在國(guó)內(nèi)多個(gè)甲醇企業(yè)發(fā)生過(guò),具體表現(xiàn)為催化劑的使用壽命≤0.5年,且粉化明顯。當(dāng)氣體中有硫(如國(guó)內(nèi)的固定床間歇造氣)過(guò)度還原生成的鐵將發(fā)生化學(xué)反應(yīng):Fe+H2S→FeS+H2。該反應(yīng)的平衡H2S很低,極易生成FeS,見(jiàn)表2。
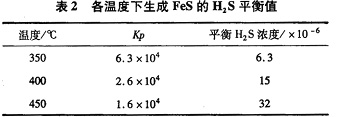
此時(shí)被還原的鐵與變換氣中的H2S反應(yīng)生成低活性的FeS。該情況下雖無(wú)烴類生成,但影響催化劑的活性,國(guó)內(nèi)企業(yè)多屬此類工況。生成的FeS與蒸汽發(fā)生下列化學(xué)反應(yīng):

在H2O及H2S含量波動(dòng)的情況下,特別是在平衡線上下波動(dòng)時(shí),催化劑在FeS與Fe3O4之間反復(fù)進(jìn)行相變。盡管催化劑活性會(huì)較好(介于FeS與Fe3O4之間),但會(huì)使催化劑的強(qiáng)度受到嚴(yán)重影響,出現(xiàn)粉化而使床層阻力增加,甚至將破碎的粉塵帶入低變段,造成低變催化劑的失活。
2.2.1 氣體含硫量較低
當(dāng)氣體的含硫量較低時(shí),有可能發(fā)生上層還原的鐵作“脫硫劑”,下層的催化劑處于“無(wú)硫氣體”工況。此時(shí)有可能發(fā)生費(fèi)托副反應(yīng),通常的表現(xiàn)是變換后甲烷含量提高,嚴(yán)重時(shí)也會(huì)生成乙炔,導(dǎo)致銅洗帶液。
2.2.2 汽氣比過(guò)低
當(dāng)汽氣比過(guò)低(≤0.3)時(shí),可能直接引發(fā)以下化學(xué)反應(yīng)。
Fe3O4+6CO→Fe3C+5CO2
5Fe3O4+32CO→3Fe3C2+26CO2
發(fā)生工況為單醇、聯(lián)醇工藝,或者開(kāi)車初期負(fù)荷很低情況下,如在合成催化劑升溫還原時(shí)或?yàn)樘岣咩~液的銅比時(shí)。此時(shí)變換出口一氧化碳含量提高,汽氣比非常低,極易引起“過(guò)度還原”繼而生成可引起費(fèi)托反應(yīng)的碳化物。一旦生成可引起費(fèi)托反應(yīng)的碳化物,在正常的工況下是不可逆的,這就是有些用戶長(zhǎng)期產(chǎn)生銅洗帶液的原因。
2.2.3 較高壓力的變換反應(yīng)
鐵鉻催化劑的活性組分Fe3O4與CO發(fā)生下列化學(xué)反應(yīng):
Fe3O4+6CO→Fe3O+5CO2
5Fe3O4+32CO→3Fe3O2+26CO2
該反應(yīng)為體積縮小反應(yīng),當(dāng)反應(yīng)壓力較高(≥2.0MPa),n(CO)/n(CO2)之比較大時(shí),容易生成鐵碳化合物,從而產(chǎn)生F-T反應(yīng),既影響活性又影響強(qiáng)度。
2.2.4 低汽氣比下的硫中毒
鐵鉻催化劑的活性組分Fe3O4與H2S可發(fā)生下列化學(xué)反應(yīng):
Fe3O4+3H2S+H2→3FeS+4H2O
△H0298=-75 kJ/mol
顯然與氣體中的蒸汽含量(汽氣比)有關(guān),其各汽氣比下的H2S平衡濃度見(jiàn)表3和圖1。
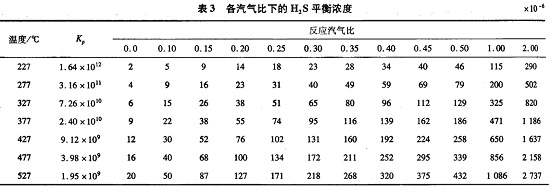
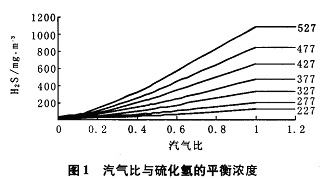
中變催化劑的產(chǎn)品說(shuō)明書(shū)都有耐硫指標(biāo),一般在400mg/m3左右,但都無(wú)相對(duì)應(yīng)的汽氣比要求。從表3及圖1中可見(jiàn),H2S與汽氣比關(guān)系很大,當(dāng)汽氣比小于0.5時(shí)其平衡的H2S急劇減少。國(guó)內(nèi)催化劑的硫中毒(或耐硫)指標(biāo)都是在某一汽氣比下才有意義。目前企業(yè)或行業(yè)標(biāo)準(zhǔn)的活性檢測(cè)的汽氣比為1.0或2.0,測(cè)試溫度為300℃。從表1可知其硫平衡值為300×10-6~700×10-6,即455~1 000mg/m3,活性檢測(cè)時(shí)耐400 mg/m3硫是沒(méi)有問(wèn)題的,因此,這種耐硫指標(biāo)對(duì)實(shí)際應(yīng)用是沒(méi)有意義的。有的中變催化劑即使在活性檢測(cè)時(shí)能耐高硫,其實(shí)也是暫時(shí)的,當(dāng)然有的催化劑添加了別的活性組分,如MoS2那就另當(dāng)別論了。
2.2.5 實(shí)際工況下的硫中毒
大部分有機(jī)硫化物在CO變換反應(yīng)過(guò)程中很快轉(zhuǎn)化為H2S。COS和CS2接近于全部轉(zhuǎn)化為H2S。
COS+H2→CO+H2S,△H0298=9.2kJ/mol
COS+H2O→CO2+H2S
△H0298=-34.7 kJ/mol
CS2+2H2O→CO2+2H2S
△H0298=-60.4 kJ/mol
硫含量一般是對(duì)總硫而言,H2S在平衡線上下大幅度波動(dòng)是危險(xiǎn)的,催化劑會(huì)在Fe3O4和FeS之間反復(fù)相變而破碎。隨著反應(yīng)的進(jìn)行,床層汽氣比逐步下降,其平衡狀態(tài)下的H2S含量也隨之下降,即抗硫性能隨之下降,出現(xiàn)下部催化劑硫中毒,而上部催化劑比較完好的現(xiàn)象。
2.2.6 各汽氣比下安全操作的硫濃度
與其他催化劑類似,由于H2S在催化劑表面發(fā)生化學(xué)吸附,盡管濃度還不足以使催化劑生成FeS,但催化劑活性卻已下降。因此,實(shí)際上引起中毒的H2S濃度應(yīng)低于平衡的H2S濃度。此外,隨著變換反應(yīng)的進(jìn)行,雖然溫度逐步升高,但床層中的汽氣比卻愈來(lái)愈低,有機(jī)硫轉(zhuǎn)化為無(wú)機(jī)硫愈來(lái)愈多,H2含量愈來(lái)愈高,其相應(yīng)允許的最高H2S含量也愈來(lái)愈少,即耐硫性能愈來(lái)愈差。由于缺乏各種鐵鉻變換催化劑的最高H2S中毒實(shí)驗(yàn)數(shù)據(jù),按傳統(tǒng)的經(jīng)驗(yàn)方法取平衡溫矩50℃。其在各汽氣比下的操作安全總S濃度見(jiàn)表4。
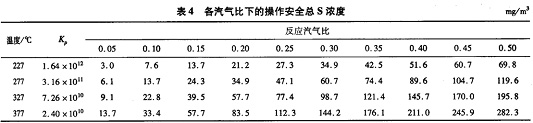
2.2.7 中低低工藝中最高耐硫含量
目前,中低低工藝出口CO體積分?jǐn)?shù)為1.5%,中變催化劑的入口溫度約為300℃,汽氣比約為0.45,則總硫應(yīng)為≤50×10-6,即≤76mg/m3。此值相當(dāng)于變換氣H2S濃度≤60 mg/m3,顯然不是所有的用戶都能夠達(dá)到的。
當(dāng)流程設(shè)置不合理,半水煤氣的CO較低,中變催化劑入口汽氣比約為0.35,則總硫應(yīng)為≤38×10-6,即≤57 mg/m3。此值相當(dāng)于變換氣H2S濃度≤44mg/m3,顯然大多數(shù)用戶都難以達(dá)到。
當(dāng)采用聯(lián)醇工藝時(shí),出口CO體積分?jǐn)?shù)為7%~5%,中變催化劑入口汽氣比約為0.30,則總硫應(yīng)為≤30×10-6,即≤45 mg/m3。此值相當(dāng)于變換氣H2S濃度≤36 mg/m3。當(dāng)流程設(shè)置不合理,進(jìn)中變的汽氣比更低時(shí),總硫則更低,這對(duì)半水煤氣脫硫來(lái)講是難以達(dá)到的,而且與后續(xù)的耐硫低變催化劑的需S工況相矛盾。
針對(duì)鐵鉻催化劑的過(guò)度還原,國(guó)外所開(kāi)發(fā)的低汽氣比鐵鉻催化劑,其核心是從動(dòng)力學(xué)上阻止或降低Fe3O4與CO過(guò)度還原反應(yīng)的速度,低汽氣比一般≥0.8。對(duì)于鐵鉻催化劑S中毒問(wèn)題國(guó)外很少報(bào)道,在此情況下一般都采用全低變工藝或在高汽氣(≥1.0)下采用中串低工藝。
綜上所述,中變催化劑在含硫氣體及低汽氣比下會(huì)發(fā)生的“過(guò)度還原”,而硫的存在避免了費(fèi)托反應(yīng)。從某種意義上講,無(wú)硫氣體的低汽氣比會(huì)引起費(fèi)托反應(yīng),使變換反應(yīng)難以進(jìn)行,而含硫又確保了低汽氣比操作的可能性。但是“不高不低”的硫含量不僅會(huì)導(dǎo)致催化劑活性下降,而且會(huì)使催化劑的強(qiáng)度受到嚴(yán)重影響,使床層阻力上升,甚至使破碎的粉塵帶入低變段,造成低變催化劑的失活,影響正常生產(chǎn)。解決的辦法是使反應(yīng)離開(kāi)FeS被H2O氧化的平衡線,以免在Fe3O4和FeS之間反復(fù)相變而破碎。對(duì)于低汽氣比下的硫中毒解決辦法同樣如此。
2.2.8 在Fe3O4活性相操作
在流程的設(shè)置上,采用高汽氣比的變換工藝,如出口CO≤0.3%的甲烷化凈化或脫碳(如MDEA)可以避免催化劑的過(guò)度還原問(wèn)題。為防止硫中毒,可根據(jù)本文提供的安全操作的S濃度指標(biāo)進(jìn)行半水煤氣脫硫,使總硫降至所要求的濃度指標(biāo),以確保在Fe3O4活性相操作。
2.2.9 在FeS活性相操作
為保持中變催化劑的強(qiáng)度,防止工況波動(dòng)而引起反復(fù)相變導(dǎo)致催化劑破碎,建議提高總硫含量,遠(yuǎn)離平衡線(高于平衡線溫度50℃),以穩(wěn)定的FeS作中變催化劑活性相,但要增加催化劑的用量1倍左右。對(duì)于變換出口CO體積分?jǐn)?shù)的1.5%的中低低工藝,中變?nèi)肟谄麣獗葹?.45,則總硫應(yīng)≥200mg/m3;對(duì)于變換出口CO體積分?jǐn)?shù)約5%的中低低聯(lián)醇工藝,中變?nèi)肟谄麣獗葹?.35,則總硫應(yīng)≥150mg/m3。
有的工廠長(zhǎng)期使用高硫煤,變換總硫相當(dāng)高,而催化劑的壽命卻不短,其理由就在于此。從中低低工藝到所謂的“中中低低工藝”,實(shí)際上就是增加中變催化劑的用量,其效果也在于此。值得注意的是變換工況一定要穩(wěn)定,汽氣比及總硫波動(dòng)會(huì)使反應(yīng)Fe3O4+3H2S+H2→3FeS+4H2O反復(fù)進(jìn)行,嚴(yán)重影響催化劑強(qiáng)度。
2.3 蒸汽用量過(guò)大導(dǎo)致阻力增加
有人以噸氨消耗蒸汽800 kg和300 kg作對(duì)比進(jìn)行了計(jì)算,以產(chǎn)氨5 t/h計(jì),則每小時(shí)多耗蒸汽2.5t。以標(biāo)準(zhǔn)流量計(jì),每小時(shí)系統(tǒng)體積增加3111m3,相當(dāng)于在15 000m3/h流量的基礎(chǔ)上增加了20%以上的體積,因此將會(huì)明顯增加系統(tǒng)的阻力。當(dāng)中變氧含量跑高時(shí),生產(chǎn)操作上習(xí)慣采用加大蒸汽用量的辦法以壓低溫度。隨著中變催化劑使用時(shí)間的延長(zhǎng),其活性不斷衰退,此時(shí)為了保證工藝指標(biāo),一般采用提高中變進(jìn)口溫度和加大蒸汽用量的辦法,易造成工況惡性循環(huán)。
2.4 投資問(wèn)題
(1)投資省(均以工業(yè)實(shí)施當(dāng)時(shí)的價(jià)格計(jì))以丹陽(yáng)化肥廠為例,若使用中變串低變工藝需投資350萬(wàn)元,而同等能力的全低變工藝僅需投資200萬(wàn)元,節(jié)省150萬(wàn)元。
(2)維修費(fèi)用低 全低變工藝不僅反應(yīng)溫度低,所需換熱面積小,而且CO-MO系催化劑活性高、壽命長(zhǎng),所需更換催化劑數(shù)量較少,故維修費(fèi)用比中串低工藝低得多。
(3)運(yùn)行費(fèi)用低 淮陰縣化肥廠是年產(chǎn)2萬(wàn)t氨的小廠,年產(chǎn)化肥8.4萬(wàn)t。與中串低工藝相比,全低變工藝在以下方面具有明顯效益:①汽耗節(jié)約(0.911-0.484)40×2=3.416(萬(wàn)元);②阻力降低,噸氨節(jié)電8 kW·h,電以0.15元/kW·h計(jì),則全年節(jié)約2.4萬(wàn)元;③每年開(kāi)車、停車10次,以每次節(jié)省時(shí)間10h計(jì),增產(chǎn)化肥84 000×10×10/7 200=1 166(t);噸肥固定成本按100元計(jì),利稅30元計(jì),1 166×130/10 000=15.16(萬(wàn)元);④省去1次脫硫后節(jié)省的電、氨、藥劑等費(fèi)用約8.0萬(wàn)元。
上述各項(xiàng)效益每年共計(jì)約60萬(wàn)元,管理較好的廠效益更加明顯。丹陽(yáng)化肥廠僅節(jié)約蒸汽一項(xiàng)半年的經(jīng)濟(jì)效益就可達(dá)到66萬(wàn)元之多。實(shí)施全低變工藝所取得的經(jīng)濟(jì)效益是十分顯著的。
3 全低變工藝的優(yōu)點(diǎn)
全低變工藝是將原中溫變換系統(tǒng)熱點(diǎn)溫度降低100℃以上,從而非常有利于一氧化碳變換反應(yīng)的平衡,實(shí)際噸氨蒸汽消耗量?jī)H為250 kg左右,且熱回收設(shè)備面積小。該工藝帶來(lái)的效益是顯而易見(jiàn)的,具體優(yōu)點(diǎn)如下。
(1)原中變催化劑用量減少1/2以上,降低了床層阻力,提高了變換爐的設(shè)備能力。
(2)床層溫度下降100~200℃,氣體體積縮小25%,降低系統(tǒng)阻力,減少壓縮機(jī)功率消耗。
(3)無(wú)費(fèi)托副反應(yīng),杜絕了生成乙炔的反應(yīng),減少銅液的消耗,從而也防止了“帶液”現(xiàn)象。
(4)換熱面積減少1/2左右。
(5)從根本上解決了中變催化劑的粉化問(wèn)題,改善了催化劑的裝卸勞動(dòng)衛(wèi)生條件。
(6)提高了有機(jī)硫的轉(zhuǎn)化能力,在相同操作條件和工況下全低變工藝比中串低或中低低工藝有機(jī)硫轉(zhuǎn)化率提高5%。
(7)操作容易,啟動(dòng)快,增加了有效運(yùn)行時(shí)間。
(8)降低了對(duì)變換爐的材質(zhì)要求。
(9)催化劑使用壽命長(zhǎng),一般可使用5年左右,最長(zhǎng)的已使用了12年;
(10)可放寬1次脫硫指標(biāo),從而降低了脫硫費(fèi)用。
近年來(lái)開(kāi)發(fā)的無(wú)飽和塔全低變流程的優(yōu)點(diǎn)更為明顯:從根本上杜絕了設(shè)備的腐蝕,減少因變換腐蝕而導(dǎo)致的停車,設(shè)備減少,系統(tǒng)的阻力降低,壓縮機(jī)出力率提高,節(jié)省了原飽和塔循環(huán)熱水泵的用電、熱水排放的能耗,降低了對(duì)設(shè)備材質(zhì)的要求。更重要的是提高了有機(jī)硫的轉(zhuǎn)化能力。因?yàn)樵趥鹘y(tǒng)的飽和熱水塔工藝中,煤氣中的各種有機(jī)硫通過(guò)循環(huán)熱水溶解,再通過(guò)變換氣釋放出來(lái),循環(huán)熱水成為有機(jī)硫的‘綠色通道’。有些工廠變換氣中存在較高的“非COS有機(jī)硫”的原因就在于此。無(wú)飽和塔流程可以解決這個(gè)問(wèn)題,不僅精脫硫中的有機(jī)硫轉(zhuǎn)化部分可以去掉,同時(shí)煤氣中非COS有機(jī)硫(常用的水解方法難以脫除)也不會(huì)串到后工段,對(duì)甲醇或合成催化劑是極為有利的。

元豐資訊:
氮肥與甲醇技術(shù)網(wǎng)
尿素網(wǎng)
造氣網(wǎng)
二甲醚網(wǎng)
尿素世界網(wǎng) (英文版)
產(chǎn)品技術(shù)庫(kù)
VIP商務(wù)俱樂(lè)部
化工論壇
QQ群大聯(lián)盟
| 會(huì)員登錄 |
網(wǎng)站地圖 |
意見(jiàn)反饋 |
關(guān)于我們 |
聯(lián)系我們 |
網(wǎng)站指南 |
法律申明 |
保護(hù)隱私權(quán) |
致作者 |
Copyright © 2008-2010 中國(guó)氮肥與甲醇技術(shù)網(wǎng) 版權(quán)所有 蜀ICP備05031754號(hào) E-mail:yf116@vip.163.com
地址:成都市青白江區(qū)怡湖芳鄰18棟8號(hào) 電話:028-83667786,83667576,89309098 傳真:028-83667578