1 前言
目前國內(nèi)UGI爐制氣的合成氨廠的變換工藝的主要特點之一是需要外加蒸汽,顯然降低蒸汽的添加量是從事研究設(shè)計科技工作者的首要任務(wù),降低蒸汽的添加量主要有以下途徑:
(1)降低反應(yīng)的汽氣比或者是水碳比(H2O/CO),大幅度降低所需回收的蒸汽量;
(2)降低設(shè)備熱損或者在同樣熱損情況下提高生產(chǎn)能力。
(3)提高反應(yīng)后多余蒸汽的回收率,這就是飽和熱水塔的技術(shù),但總有一個效率問題,理論與實踐表明僅能達(dá)到~60%;
上述的前面兩點要依靠催化劑及變換反應(yīng)工藝的進(jìn)步,上世紀(jì)80年代上海化工研究院開拓了這方面的工作,作出了杰出貢獻(xiàn),他們開發(fā)的混碾法生產(chǎn)鈷鉬耐硫低變催化劑串在傳統(tǒng)的中變爐后的串低變工藝(中串低)使變換外加蒸汽消耗大幅度下降,生產(chǎn)能力也有所提高,1986年湖北省化學(xué)研究院用浸漬法生產(chǎn)了活性更好而成本較低的B302Q、B303Q催化劑,并對中串低工藝進(jìn)一步完善,1989年也對中低低工藝進(jìn)行了探討,由于中低低本質(zhì)上仍是中串低,但其反應(yīng)的汽氣比更低,而反應(yīng)汽氣比的降低會危害中變催化劑的性能從而影響正常生產(chǎn),因此我們重點研究全低變工藝。所謂全低變工藝就是全部使用耐硫變換催化劑的“全低變工藝”,各段進(jìn)口溫度均為200℃左右。在相同操作條件和工況下其設(shè)備能力和節(jié)能效果都比原各種形式的中串低、中低低要好。
2 早期全低溫變換
1989年與湖北省化肥公司共同開發(fā)的全低變工藝是采用中串低的催化劑,無抗毒、抗低硫性能,開車初期的各項操作指標(biāo)明顯優(yōu)于中串低或中低低,使噸氨蒸汽消耗下降一半,能力提高一倍。由于但對鈷鉬催化劑的中毒規(guī)律認(rèn)識不夠,工藝上解決措施不多,導(dǎo)致工業(yè)應(yīng)用中出現(xiàn)催化劑失活等問題。這些問題在1991~1994年期間我院經(jīng)過研究全部解決[3],使得這一工藝在行業(yè)得到迅速推廣。
1995~2000年期間化肥行業(yè)出現(xiàn)以下主要問題有①不具備開發(fā)全低變技術(shù)的催化劑生產(chǎn)單位也開始推廣全低變工藝。據(jù)不完全統(tǒng)計,先后有5個生產(chǎn)耐硫變換催化劑的單位在10多家中小型企業(yè)進(jìn)行全低變工藝的工業(yè)應(yīng)用實施工作均以失敗告終。②在這些失敗的案例發(fā)生以后少數(shù)行業(yè)人員在不明白失敗的真實原因情況下,在不同的場合發(fā)表了一些不正確的觀點,特別是對全低變技術(shù)作出了一些不科學(xué)的評價。③有些企業(yè)對全低變的一些技術(shù)細(xì)節(jié)重視不夠,操作控制不嚴(yán)也影響了全低變技術(shù)的經(jīng)濟(jì)效益。
理論研究與實踐使用表明鈷鉬催化劑是會中毒的,我國中小合成氨廠的原料氣為固定床間歇法制氣工藝,該工藝包括制氣和吹風(fēng)的氧化、蒸汽分解、變換等反應(yīng),其中既有放熱反應(yīng)又有吸熱反應(yīng),造氣過程溫度波動也較大,所使用的固體燃料有無煙煤、焦炭及各種煤球(碳化煤球,粘土、陶土煤球、焦油煤球,紙漿煤球及清水棒)化學(xué)組成極其復(fù)雜。生成的半水煤氣中有大量雜質(zhì),經(jīng)洗滌、脫硫后仍含有少量雜質(zhì)進(jìn)入變換系統(tǒng),經(jīng)分析有氰氫酸、氨基甲酸、丙烯醛、亞氨基、乙酸及羰基化合物…等等。以上某些化合物對Co-Mo耐硫變換催化劑有明顯毒害作用,為此研制了保護(hù)催化劑用的抗毒劑。特別要說明的是所謂“抗氧劑”的提法是不正確的,Co-Mo變換催化劑都是抗氧的,否則就不能用含0.5%氧的半水煤氣進(jìn)行硫化了,由于抗毒劑也有促進(jìn)氧與氫、一氧化碳的反應(yīng),所以往往有一定的溫升,也就俗稱為“抗氧劑”了。
3 目前采用的工藝流程
全低變技術(shù)經(jīng)過湖北省化學(xué)研究院17年的研究、摸索和實踐,在催化劑及工藝上都取得長足的進(jìn)步,日趨完善,最長已使用十二年,現(xiàn)推薦流程如下,如圖1:
目前“全低變”工藝在全國二百多家中、小氮肥廠運(yùn)行,最長達(dá)12年之久,被列入“九五”化工國家科技成果重點推廣計劃項目。僅中型廠及8萬噸以上的合成氨廠就有36家,值得一提的是,山西某化肥廠共有三套變換裝置,分別為中串低、中低低、全低變,經(jīng)過三年的運(yùn)行比較,全部改成了全低變流程,其中包括采用‘軸徑向’的中低低變換裝置。該流程的主要優(yōu)點:
(1)杜絕了鐵鉻中變催化劑過度還原的問題,延長了一段變換催化劑的使用壽命;
(2)床層溫度下降了100~200℃,氣體體積縮小25%,降低系統(tǒng)阻力,提高了變換爐的設(shè)備能力;減少壓縮機(jī)功率消耗;
(3)高有機(jī)硫的轉(zhuǎn)化能力,在相同操作條件和工況下全低變工藝比中串低或中低低工藝有機(jī)硫轉(zhuǎn)化率提高5個百分點;
(4)操作容易,起動快,增加了有效時間;
其具體應(yīng)用工業(yè)實例都有報導(dǎo)
4 取消飽和塔的全低變工藝
我們注意到,隨著低溫變換技術(shù)的采用,特別是全低變工藝的應(yīng)用,變換氣中過量蒸汽已經(jīng)很少。也就是,利用飽和熱水塔熱水塔回收潛熱的意義也就不大了。計算表明當(dāng)變換出口CO為1.2%時飽和塔可回收的潛熱為噸氨~200公斤蒸汽,而當(dāng)聯(lián)醇工藝變換出口CO為4%時飽和塔可回收的潛熱僅為噸氨65公斤蒸汽。假如在流程上用噴水增濕來代替水加熱器回收變換氣的顯熱,而用外加蒸汽代替回收的潛熱,即聯(lián)醇工藝噸氨蒸汽消耗增加65公斤,這樣聯(lián)醇工藝完全可取消飽和熱水塔;而出口CO為1.2%的變換工藝的噸氨蒸汽消耗增加~200公斤,其潛熱可設(shè)法用其它方法回收,如:保留熱水塔,熱水用于銅洗再生器,兩者蒸汽消耗總和低于有飽和熱水塔流程,而操作及設(shè)備費(fèi)用卻大幅度下降。
取消飽和塔后,由于半水煤氣的氧與硫化物處于無水情況,而熱水塔的循環(huán)水不與煤氣接觸,不含有氧,也就是使變換系統(tǒng)水、氣相分別處于“有氧則無水,有水則無氧”的“非腐蝕”狀態(tài),從而杜絕由于飽和塔引起的各種問題。整個變換溫度控制都用噴水增濕量來調(diào)節(jié),徹底解決了用水加熱器換熱工藝中的設(shè)備腐蝕快、材質(zhì)要求高、進(jìn)出口管線、閥門多的問題。同時由于噴水增濕的熱損小于水加熱器,加上沒有了飽和熱水塔的熱水排放,其熱量(蒸汽)回收率高。
特別要指出的是:變換工段的低變爐出口的有機(jī)硫一般為~0.5ppm,但變換系統(tǒng)出口都為2~3ppm(這就需要專門配置精脫硫),究其原因是傳統(tǒng)的變換系統(tǒng)都采用了飽和熱水塔工藝,煤氣中的各種有機(jī)硫通過循環(huán)熱水溶解,再通過變換氣釋放出來,循環(huán)熱水成為有機(jī)硫的‘綠色通道’,有些工廠精脫硫出口存在較高的‘非COS有機(jī)硫’,可能就是此原因。
如果采用無飽和塔流程就不存在這個問題,精脫硫部份可以簡化。同時煤氣中的非COS有機(jī)硫(常用的水解方法難脫除)也不會串到后工段,對甲醇或合成催化劑是極有利的。
上述工藝要求變換氣的最低硫化氫(總硫)含量為~120mg/NM3,如改變蒸汽加入位置,可降為~100mg/NM3;若將三段催化劑分為四段裝填,則最低硫化氫(總硫)含量降為~80mg/NM3,與傳統(tǒng)的中串低或中低低工藝相同。
4.1 流程示意圖
取消飽和塔流程的流程如圖2,此時熱水塔出口的變換氣溫度~40℃。
4.2 目前的工業(yè)應(yīng)用
無飽和熱水塔工藝用戶:
(1)南京化工廠,2萬噸,1998年應(yīng)用。
(2)河北冀州化肥廠,4萬噸,2001年12月應(yīng)用。
(3)山西原平化肥廠,10萬噸,2002年1月應(yīng)用。
(4)湖南湘潭,16萬噸,2004年6月應(yīng)用。
(5)安徽太和,5萬噸,2004年12月。
(6)山東章丘二化5萬噸,2005年1月。
(7)越南社會主義共和國河北化工氮肥廠,10萬噸,
(8)山西晉豐煤化工有限責(zé)任公司聞喜14萬噸,2005年4月應(yīng)用。
(9)貴州化肥廠13萬噸,2005年1月應(yīng)用。
(10)山西晉豐煤化工有限責(zé)任公司高平17萬噸,2005年12月應(yīng)用。
(11)河南新鄉(xiāng)化肥總廠23萬噸。
5 用噴水增濕取代填料的飽和熱水塔的全低變工藝
5.1 取消填料可行性
各種各樣的填料在飽和熱水塔在變換工段已延用多年,其作用是提高氣液接觸面積,加快氣液兩相的平衡,但此設(shè)備本身存在填料多,阻力大的弊病是無法克服的。往往影響變換系統(tǒng)能力的提高。要提高變換系統(tǒng)的能力往往只有重新制造一個較大的飽和熱水塔。由于填料是造成飽和熱水塔阻力的主要原因。最近開發(fā)成功的取消飽和熱水塔工藝提示我們,飽和熱水塔的回收的熱量已愈來愈少,填料的作用也已愈來愈小,這為取消填料創(chuàng)造了條件。
5.2 高效霧化噴頭
噴頭的霧化度對氣液間的傳熱傳質(zhì)效率影響極大,設(shè)計中采用國外引進(jìn)自行生產(chǎn)的高效霧化噴頭全部取代傳統(tǒng)填料,該噴頭不同于傳統(tǒng)“傘狀水膜狀”為撞擊式,霧化度極高,水珠粒度為0.1mm,1M3水霧化成lmm的液滴,其表面積增大1000倍,霧化成0.1mm的液滴,其表面積增大10000倍,極大提高飽和熱水塔的水氣間的傳熱傳質(zhì)效率。
5.3 流程示意圖
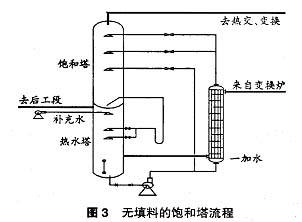
去掉飽和塔的填料,在塔內(nèi)設(shè)置多層高效霧化噴頭,將熱水塔、一水加出來的熱水增壓后進(jìn)入高效霧化噴頭噴成霧狀與進(jìn)入的半水煤氣混合增濕,以提高半水煤氣的含濕量,也就是回收熱水中的熱量,多余的溫度較低的水進(jìn)入熱水塔。
去掉熱水塔的填料,在塔內(nèi)設(shè)置多層高效霧化噴頭,將飽和塔出來的溫度較低的水加壓進(jìn)入高效霧化噴頭噴成霧狀與進(jìn)入熱水塔的溫度較高的(接近露點)變換氣混合,使變換氣冷凝“下雨”,生成熱水部分直徑進(jìn)入飽和塔下層,一水加熱器。
5.3.1 該工藝的優(yōu)點
1)熱量回收不低于填料式。
2)節(jié)省大量的填料投資,目前填料多為不銹鋼材料,其效益可觀。
3)由于無填料,克服了塔盤、填料等易堵塞的缺點,使操作會維護(hù)變得非常簡便。
4)氣體流動阻力大幅度減少,設(shè)備能力也就大幅度增加。
5.3.2工業(yè)應(yīng)用
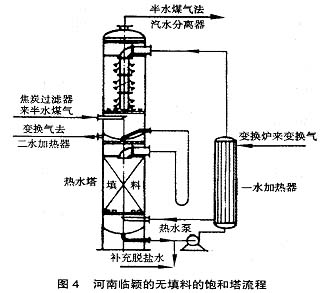
目前正在河南臨穎6萬噸合成氨廠應(yīng)用五年[13],由于擔(dān)心飽和塔熱水出口與熱水塔熱水進(jìn)口壓差小,難以保證噴嘴在熱水塔中的使用效果,僅在飽和塔使用噴嘴代替填料,如下圖,采用霧化噴嘴飽和塔系統(tǒng)壓差0.03MPa,另一套填料塔為0.06MPa,出飽和塔半水煤氣與熱水溫度相差4~5℃;變換蒸汽消耗200kg/tNH3,變換氣CO含量1.6%,飽和塔回收蒸汽、降低阻力達(dá)到了理想水平。
實際上飽和塔熱水出口與熱水塔熱水進(jìn)口有0.02MPa壓差,半水煤氣與變換氣有0.03MPa的壓差,總共有0.05MPa壓差,噴嘴完全可使用在熱水塔,只是噴嘴的形式與飽和塔不同。
此外,湖北新生源公司(湖北公安縣)應(yīng)用四年。還有河南正陽氮肥廠,浙江開化清華化工。
6 用于單醇的變換兼有機(jī)硫轉(zhuǎn)化的全低變工藝
單醇生產(chǎn)中原料氣都為水煤氣,其組分為:CO-38%;CO2-6%;H2-50%。變換出口CO含量20~25%左右,反應(yīng)的汽氣比更低,其T(溫度)—R(汽氣比)的CO平衡計算見表1:
從表中可知,在出口CO為22%時,其總汽氣比很低~0.14。是不能用中變催化劑,必需用鈷鉬低變催化劑,而用鈷鉬低變催化劑其反應(yīng)汽氣比低、溫度低、催化劑空速低對有機(jī)硫轉(zhuǎn)化不利,為此需要配置有機(jī)硫轉(zhuǎn)化(爐)段。
6.1 變換熱交換器后串中溫水解爐
流程應(yīng)用:河南尉氏,應(yīng)用3年,出口COS~0.2mg/m3。
6.2 變換爐內(nèi)串高溫水解爐
該流程適用于非COS及高硫原料氣的轉(zhuǎn)化,流程應(yīng)用:湖北中天,應(yīng)用4年,出口COS~0.5mg/m3。高硫原料氣用戶:四川高縣進(jìn)口的有機(jī)硫>500mg/NM3。

元豐資訊:
氮肥與甲醇技術(shù)網(wǎng)
尿素網(wǎng)
造氣網(wǎng)
二甲醚網(wǎng)
尿素世界網(wǎng) (英文版)
產(chǎn)品技術(shù)庫
VIP商務(wù)俱樂部
化工論壇
QQ群大聯(lián)盟
地址:成都市青白江區(qū)怡湖芳鄰18棟8號 電話:028-83667786,83667576,89309098 傳真:028-83667578