1 前言
微量硫?qū)状、甲烷化、氨合成催化劑的中毒及對脫碳溶劑,銅洗溶液、設(shè)備腐蝕與尿素安全生產(chǎn)等的危害是長期制約合成氨生產(chǎn)的瓶頸,大量的研究與實踐表明在合成氨生產(chǎn)中原料氣必須進行精脫硫,即總硫<0.1×10-6,才能實現(xiàn)長期的高產(chǎn)、穩(wěn)產(chǎn)。
國外自1987年英國ICI公司提出水解催化劑串氧化鋅的工藝以后,在常溫干法精脫硫領(lǐng)域內(nèi)進展不大,這主要由于發(fā)達國家的氮肥廠大多是以天然氣制取的,采用傳統(tǒng)的高溫精脫硫工藝已相對穩(wěn)定。即使是在煤制原料氣中,因企業(yè)規(guī)模以大型為主,采用低溫甲醇洗能達到氣體凈化與精制要求(包括脫除總硫<0.1×10-6),因此干法常溫精脫硫只是作為一種補充手段。我國的情況正相反,中小氮肥廠大多以煤為原料,一般認為規(guī)模小于20萬噸氨/年的氮肥廠采用低溫甲醇洗工藝是不經(jīng)濟的,因此增設(shè)干法常溫精脫硫是必須的,常溫精脫硫新技術(shù)的開發(fā)、產(chǎn)業(yè)化及使用技術(shù)的研究還應(yīng)當由我國的科技、工程人員來完成。
在過去的20年,我國常溫精脫硫的研究被很多專家認為是脫硫領(lǐng)域內(nèi)最為活躍的一個分支。太原工業(yè)大學(xué)、西北化工研究院、昆山精細化工研究所等均做了很多工作,我中心獨辟蹊徑,提出水解串特種活性炭的常溫精脫硫路線于1991年最早實現(xiàn)工業(yè)應(yīng)用,進而開發(fā)了一套較為完整的以JTL-1、JTL-4、JTL-5新工藝為核心的常溫精脫硫(ATFSR)新技術(shù)。該新技術(shù)可以解決以煤或重油制氣的各種工況下的精脫硫(總硫H2S+COS+CS2<0.1×10-6)。我國政府于1999、2000年舉行兩屆ATFSR新技術(shù)國際培訓(xùn)班,獲得中國發(fā)明專利23項,有4篇論文參加國際氮(化)肥會議,先后有8種精脫硫劑產(chǎn)品出口至美、英、澳大利亞等國家,在全國小氮肥第12次技術(shù)交流會上已全面介紹ATFSR新技術(shù)的特點,組成與工業(yè)應(yīng)用,本文重點介紹該新技術(shù)在過去的5年中的最新進展。
2 保護甲醇催化劑
2.1 聯(lián)醇工藝甲醇催化劑使用壽命與生產(chǎn)強度的新進展
合成氨聯(lián)產(chǎn)甲醇是中國獨創(chuàng)的工藝,1993年以前,干法脫硫技術(shù)落后,聯(lián)醇催化劑壽命低,僅為2~3個月,導(dǎo)致這一新工藝的優(yōu)勢得不到體現(xiàn)。表1與圖1的數(shù)據(jù)說明:經(jīng)過10多年特別是近5年常溫精脫硫新技術(shù)的應(yīng)用(加上均溫型內(nèi)件的配套使用與管理加強等因素),保護甲醇催化劑所取得的業(yè)績最為成功,遠遠超過原來的預(yù)期目標,單塔聯(lián)醇催化劑的壽命與生產(chǎn)強度都提高了5~10倍。這5年的進展也充分證明了聯(lián)醇工藝對氮肥行業(yè)的重要貢獻:
1)聯(lián)產(chǎn)甲醇工藝實現(xiàn)了長周期穩(wěn)產(chǎn)高產(chǎn)與真正意義的工業(yè)化,成為“中國特色,世界水平”與化肥工業(yè)史上的創(chuàng)舉[3]得到了充分體現(xiàn)。
2)實現(xiàn)了合成氨生產(chǎn)的長周期穩(wěn)產(chǎn)高產(chǎn)并有重大的節(jié)能降耗作用。
3)對中小化肥廠產(chǎn)品結(jié)構(gòu)得到有效調(diào)整,顯著提高經(jīng)濟效益與競爭力。
4)聯(lián)產(chǎn)一碳化工,成為綜合化工企業(yè):
5)促進聯(lián)氨等新工藝的開發(fā)。
2006年前后,聯(lián)醇生產(chǎn)又取得歷史上2項最好的成績:一是山東平度化肥廠的單塔聯(lián)醇催化劑的壽命突破4年,達到4年4個月,接近表3國外單醇催化劑的壽命5年的水平,至于甲醇催化劑的生產(chǎn)強度,由于工藝不同,聯(lián)醇無法與單醇比較生產(chǎn)強度的數(shù)據(jù)。二是山西豐喜集團聯(lián)醇的甲醇催化劑使用壽命達3年,生產(chǎn)強度即每m3催化劑生產(chǎn)甲醇9270噸,創(chuàng)聯(lián)醇歷史最高紀錄,年減少運行費用181萬元,年增產(chǎn)合成氨4500噸,增加產(chǎn)值近1000萬元,運行水平居國內(nèi)最好成績之一。
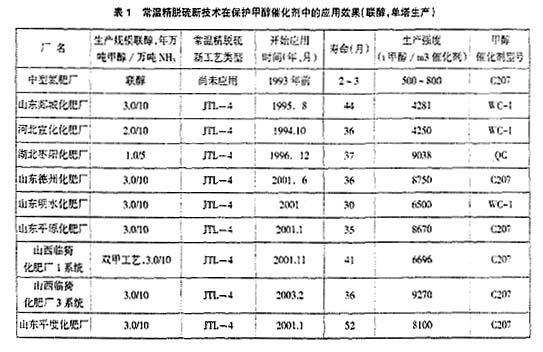
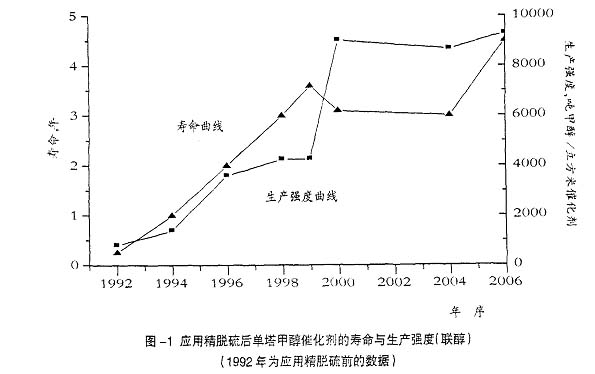
2.2 單醇生產(chǎn)中的精脫硫技術(shù)(EH-2中溫耐硫水解催化劑+JTL-1夾心餅工藝)
單醇生產(chǎn)中CO變換和CO2脫碳是部份變換(出口CO為18~22%)和部份脫碳(出口CO2為1~4%)。因CO變換率(~30%)大幅度降低,導(dǎo)致變換氣中有機硫(主要是COS)含量提高10倍左右,不僅會污染脫碳溶液,還因CO2脫除率降低而導(dǎo)致脫碳氣中有機硫(主要是COS)增高,加重了脫碳后常溫精脫硫的負荷。因此在單醇生產(chǎn)中,不論變換是采用Fe-Cr中變催化劑還是采用Co-Mo寬變催化劑、不論采用何種脫碳工藝、為脫除較高含量的有機硫COS,我們開發(fā)的單醇生產(chǎn)中的精脫硫由EH-2中溫耐硫水解催化劑+JTL-1夾心餅工藝組成的精脫硫技術(shù)均可適用多種形式的單醇,并取得有效的效果。
精脫硫工藝流程示意圖如下:
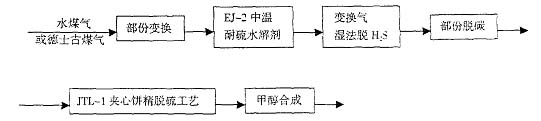
EH-2中溫耐硫水解催化劑的串聯(lián)使用位置有二種方案可供選用:
1)EH-2催化劑放在變換后面的適宜位置(即變換爐外),類似于“中變串低變工藝”爐外串聯(lián)模式,如上述流程示意圖。
2)EH-2催化劑的位置也可放在變換爐內(nèi)最后一段類似于“中變串低變工藝”爐內(nèi)串聯(lián)模式,流程示意圖如下:
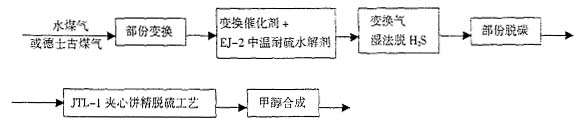
上述二種方案的作用與效果相同,需要注意的是選擇合適的EH-2催化劑使用條件(如溫度)。
1995年針對魯南化肥廠10萬t甲醇/年項目設(shè)計中提出的部份變換后高含量COS的脫除問題,我中心開發(fā)新型的EH-2抗硫酸鹽化有機硫水解催化劑(后改名為EH-2中溫耐硫水解催化劑),列為原中國石油化工總公司的重點項目,于1998年通過該總公司主持的技術(shù)鑒定,并獲得中國發(fā)明專利。表2列出的EH-2中溫耐硫水解催化劑的使用數(shù)據(jù)清楚表明,其COS轉(zhuǎn)化率在200℃時可高達90~95%,接近該工況下的平衡轉(zhuǎn)化率,保證了整個精脫硫工藝的暢通。
2.3 單醇工藝甲醇催化劑使用壽命與生產(chǎn)強度的新進展
我國以煤為原料低壓生產(chǎn)甲醇(單醇)是近10年開始興起的,低壓單醇工藝中甲醇催化劑使用壽命與生產(chǎn)強度的數(shù)據(jù)見表3。
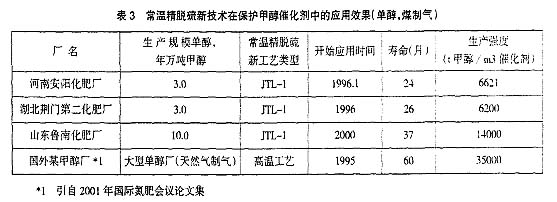
從表3數(shù)據(jù)可以看出,山東魯南化肥廠甲醇催化劑的使用創(chuàng)國內(nèi)最好成績,壽命達37個月,生產(chǎn)強度達14000t甲醇/m3催化劑,雖與國外的水平有一定差距,但是魯南等化肥廠生產(chǎn)單醇的歷史很短,還不到10年時間,各方面均缺乏經(jīng)驗,圖1的結(jié)果表明,再經(jīng)10~20的努力,我國以煤為原料低壓單醇生產(chǎn)中甲醇催化劑的使用可以接近或達到國際先進水平。
3 保護甲烷化與氨合成催化劑
銅洗工段在國外已被淘汰五、六十年,我國過去沒有常溫精脫硫技術(shù),中小氮肥廠不得不采用它。該工段操作穩(wěn)定性差,特別是產(chǎn)生的重金屬離子(Cu++)對地下水的污染更是環(huán)保所不允許的。表4的數(shù)據(jù)證明,采用常溫精脫硫新技術(shù)后,甲烷化催化劑的壽命達8年接近或達到大型氮肥廠的水平。最近隨著甲醇—甲烷化“雙甲”工藝的迅速推廣,落后的銅洗工段將被完全取代。
大型氮肥廠氨合成催化劑壽命可大于10年。采用常溫精脫硫新技術(shù)后,中小氮肥廠的氨合成催化劑壽命均有成倍延長,如山東郯城化肥廠(10萬tNH3/a)使用的氨合成催化劑的壽命已達到7年。湖南安淳公司最先提出的甲醇—甲烷化流程對以煤為原料的中小氮肥廠的工藝有重大改進,與常溫精脫硫新技術(shù)相結(jié)合后,氣體凈化精制又提高到新水平,現(xiàn)在單塔甲醇催化劑壽命可達3~4年,單一的甲烷化催化劑(非甲醇—甲烷化工藝)壽命達8年,可以期望再經(jīng)~10年,銅洗工段將徹底被淘汰,甲烷化催化劑、氨合成催化劑的壽命可達到大型廠水平即10年左右。
4 保護尿素脫氫催化劑與尿素脫氫新技術(shù)
全國小氮肥第12次技術(shù)經(jīng)驗交流會上介紹我中心開發(fā)的尿素脫氫新技術(shù)(由常溫精脫硫+TH-2、TH-3脫氫催化劑+HC-2微量硫分析儀組成)以來,形勢發(fā)生以下的重大變化:
1)國家對安全生產(chǎn)、清潔、環(huán)保友好型生產(chǎn)高度重視
2)2005年某廠尿素合成塔發(fā)生重大的爆炸事故,雖然對事故的原因沒有明確的結(jié)論,但化工工藝專家均認為不能排除尿素合成高、中壓尾氣H2、O2含量積累引起的化學(xué)爆炸的原因。曾有專家調(diào)查,這一化學(xué)爆炸在我國中型尿素工段幾乎每一部位都發(fā)生過,屬特大事故的爆炸已有10余次。
3)國際上過去尿素生產(chǎn)的兩種主要工藝即CO2氣提與氨氣提工藝經(jīng)長期比較后,現(xiàn)在CO2氣提工藝占為優(yōu)勢(我國水溶液全循環(huán)法工藝實際上是CO2氣提工藝的前身)。對于CO2氣提工藝,國際上公認必須采用貴金屬尿素脫H2催化劑以徹底消除H2、O2積爆的爆炸事故。
4)5年來相關(guān)的技術(shù)出現(xiàn)了重大進步
●四川美豐化肥廠(天然氣為原料,CO2氣中總硫<0.1 ×10-6)TH-3尿素脫H2催化劑首次使用達到5年,與國外使用8~10年的水平相比已前進一大步。
●以煤為原料的中、小氮肥廠的脫硫比以前重視多了,普遍設(shè)置“半脫”—“變脫”—“精脫”,設(shè)置“變脫”后,尿素系統(tǒng)的CO2氣體中精脫硫負荷與年操作費用均可降低很多,使尿素脫氫新技術(shù)在煤制尿素廠中得到進一步的推廣。
●尿素脫氫技術(shù)的進步:脫氫反應(yīng)熱量加熱回收技術(shù),與中壓脫氫即將實施,可十分顯著地降低脫氫的操作費用。
●TH-3尿素脫氫催化劑的常溫再生專利技術(shù)已在鎮(zhèn);蕪S應(yīng)用成功,壽命達9個月(超過預(yù)定指標6個月),也為尿素脫氫新技術(shù)的推廣創(chuàng)造了十分有利的條件。
由于上面的原因,近幾年來,使用脫氫技術(shù)的廠家如晉豐集團高平分公司與聞喜分公司、中化天脊集團高平分公司、中石油寧夏分公司、烏魯木齊分公司等公司已明顯增加,對以煤為原料的中小氮肥廠采用由精脫硫+TH-2/TH-3脫H2催化劑+HC-2微量硫分析儀組成的尿素脫氫新技術(shù)不僅徹底消除H2-O2積累的爆炸隱患,節(jié)約氨耗達1.5~2kg/t尿素,同時徹底消除硫?qū)ιa(chǎn)系統(tǒng)的設(shè)備腐蝕,實現(xiàn)了尿素生產(chǎn)安全、清潔、環(huán)保友好的目標[6]。
5 常溫精脫硫與THC—1脫烴催化劑在食品CO2中的應(yīng)用
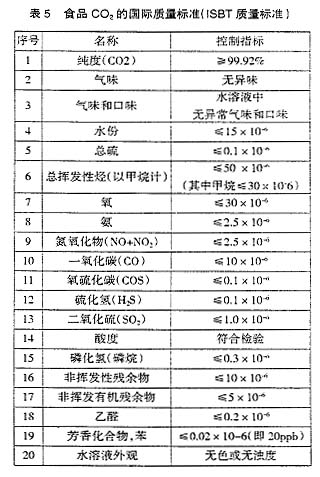
食品CO2是近年來發(fā)展迅速的行業(yè),可用于飲料、煙絲膨化、超臨界萃取、蔬菜保鮮等領(lǐng)域。據(jù)一外國公司介紹,美國用于飲料行業(yè)的食品CO2年銷售量為約320萬噸(占食品CO2總銷量的30~40%),中國的人口是美國的5倍,保守的估算中國食品CO2的年需求量在5年后將可能超過1000萬噸,因此尚有很大的發(fā)展空間。過去中國的食品CO2標準很粗放,借與國際接軌,以求高的效益,現(xiàn)在很多食品CO2廠都開始執(zhí)行國際飲料技術(shù)協(xié)會規(guī)定的ISBT質(zhì)量標準(見表5)。由表5可知,食品CO2的ISBT質(zhì)量標準十分苛刻,指標共有20項,其純度要求高,雜質(zhì)的含量很低,均為10-6(下又稱ppm)或10-9(下又稱ppb)級。上述20項指標中最苛刻的是下面3項:
1)總硫≤0.1×10-6
2)苯含量≤0.02×10-9(即20ppb)
3)總揮發(fā)性烴含量(以CH4計,下簡稱總烴)≤50×10-6(其中CH4≤30×10-6)
5.1 常溫精脫硫在這里有雙重任務(wù):一是食品CO2 ISBT質(zhì)量標準中4項指標涉及精脫硫,必須達到;二是為實現(xiàn)總烴、苯、乙醛3項達標所采用的貴金屬脫烴催化劑必須有精脫硫保護,才能有長的使用壽命。在CO2~l00%(即106ppm的原料氣中脫除微量有機硫cos(~10ppm)的原理為水解反應(yīng):
COS+H2O=CO2+H2S
受高含量CO2的平衡制約,要求有更好活性的水解催化劑,我中心開發(fā)的T504及其改進型T504A水解催化劑串T103特種活性碳的JTL—1新工藝已在全國40多廠應(yīng)用,還應(yīng)用到美國BOC、澳大利亞BOC公司。
5.2 THC-1脫烴催化劑的開發(fā)及其應(yīng)用
我中心孔渝華研究員于1991、2001年2次去美國與BOC公司美國技術(shù)中心及WiTTemann公司(專為食品CO2生產(chǎn)廠提供設(shè)計,設(shè)備等)交流時,他們均采用貴金屬脫烴催化劑的催化氧化方法脫除烴類。盡管它的價格高,但最大優(yōu)點是可使CO2原料氣中的各種烴脫除達到ISBT質(zhì)量標準,另外壽命長(3~5年)、空速高、可以做到自熱平衡不外加熱源生產(chǎn),故是目前國際上被采用的有效方法。
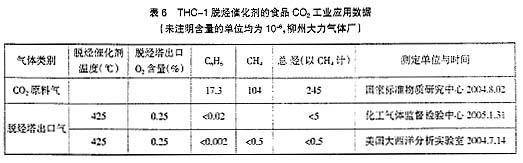
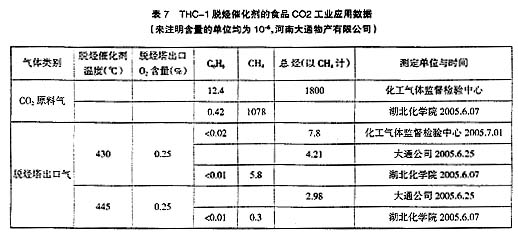
經(jīng)多年努力,2003年以來我中心開發(fā)的THC-1脫烴催化劑已在柳州大力氣體廠、濟南化肥廠等6個食品CO2廠進行工業(yè)應(yīng)用,并有4個廠的食品CO2產(chǎn)品經(jīng)國家法定單位測定質(zhì)量指標達到IMST質(zhì)量標準,有關(guān)脫烴的數(shù)據(jù)見表6、表7。表6、表7的數(shù)據(jù)指出,國內(nèi)多家權(quán)威單位與美國大西洋實驗室的測定結(jié)果相吻,THC-1脫烴催化劑在425~445℃間對CH4與苯的脫除有很高的活性,脫烴后凈化氣中總烴、CH4與苯含量分別小于7.8×10-6、5.8×10-6與0.02×10-6,達到ISBT質(zhì)量標準(分別小于50×10-6、20×10-6與0.02×10-6),即使在CO2原料氣中總烴含量高達1800×10-6,苯含量高達17.3×10-6時均達到滿意結(jié)果。
杭州快凱高效節(jié)能有限公司與我中心合作開發(fā)的“國際質(zhì)量標準的食品級CO2生產(chǎn)技術(shù)”已于2005年12月通過浙江省科技廳主持的專家鑒定,鑒定意見為技術(shù)水平“國內(nèi)領(lǐng)先,國際先進”,常溫精脫硫新工藝、THC-1脫烴催化劑與內(nèi)件組成的脫烴工藝是該生產(chǎn)技術(shù)的難點與創(chuàng)新點。
6 T504常溫水解保護技術(shù)在高含量COS原料氣中的應(yīng)用[8]
煙臺萬華集團為國內(nèi)首家MDI(二苯基甲烷二異氰酸酯、多亞甲基多苯基異氰酸酯)的生產(chǎn)廠家,目前年產(chǎn)已達10萬噸。該公司CO造氣車間生產(chǎn)的CO原料氣中COS含量高達1000~2000ppm,要保證后序工段的正常生產(chǎn)及MDI產(chǎn)品質(zhì)量,必須要將CO中的硫化物脫除,而在此工藝下高COS脫除的難度較大。過去采用常溫水解串氧化鐵工藝,水解催化劑與氧化鐵脫硫劑更換頻繁,脫硫費用高,且難以保證后工序?qū)α蚝康囊蟆T摴鞠群笈c國內(nèi)多家脫硫劑生產(chǎn)廠家合作攻關(guān),經(jīng)過近一年的工業(yè)側(cè)流實驗后,選擇了湖北省化學(xué)研究院氣體凈化中心的常溫水解保護技術(shù):流程如下:

工藝參數(shù):氣量2700M3/h
CO 98%,CO20.3%,H20.2%
COS 1000~1500ppm H2S100~200ppm
從2004年11月新工藝投入運行以后,至2005年10月,在大修期間,由于設(shè)備檢修,考慮T504水解催化劑已使用1年而提前更換,T504水解劑在更換前仍有較好活性,水解塔溫度保持≤70℃,出口COS≤100ppm,達到CO凈化氣脫硫指標,該公司對T504常溫水解保護技術(shù)與過去的脫硫工藝進行效益對比,見表8。
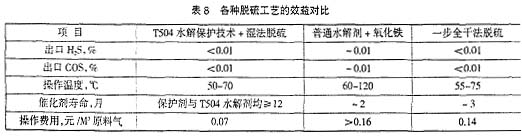
從表清楚看出采用T504水解保護技術(shù)串濕法脫硫可以較好地解決了高CO高COS工況下脫除COS的難題,其具有如下特點:
1、脫硫效果好,出口H2S<0.01%,COS<0.01%。
2、操作溫度低,50~70℃,比普通水解催化劑降低了能耗。
3、使用周期長,大于12個月,是普通水解串氧化鐵的3~4倍,減少了開停車帶來的產(chǎn)能損失
4、操作費用低,T504水解保護技術(shù)串濕法脫硫的總脫硫費用為0.07元/M3,僅為一步法的1/2、為普通水解串氧化鐵的2/5,經(jīng)濟效益顯著。
5、可耐受高COS的沖擊(進口COS達0.5%時,出口仍保證H2S<0.01%,COS<0.01%)。

元豐資訊:
氮肥與甲醇技術(shù)網(wǎng)
尿素網(wǎng)
造氣網(wǎng)
二甲醚網(wǎng)
尿素世界網(wǎng) (英文版)
產(chǎn)品技術(shù)庫
VIP商務(wù)俱樂部
化工論壇
QQ群大聯(lián)盟
地址:成都市青白江區(qū)怡湖芳鄰18棟8號 電話:028-83667786,83667576,89309098 傳真:028-83667578