[摘 要] 論述了雙甲(醇烴化)工藝因地制宜設(shè)計的幾種類型工藝及不同的設(shè)計壓力和工程的有關(guān)配置方式,介紹和分析了對工程問題的思考方法及處理問題的方式,并對各種模式的工程設(shè)計進行了較詳細介紹和經(jīng)濟效益、環(huán)保效益的初步分析。
[關(guān)鍵詞] 雙甲工藝;醇烷化;醇烴化;工程設(shè)計;分析
0 前言
獲得了國家科技進步二等獎的技術(shù)——合成氨原料氣雙甲凈化精制工藝(簡稱雙甲工藝或醇烷化工藝)為我國自主知識產(chǎn)權(quán)的發(fā)明技術(shù),是以謝定中教授為首的湖南安淳高新技術(shù)有限公司技術(shù)人員經(jīng)過近二十年的不懈努力創(chuàng)造的技術(shù)。
從1992年第一套工業(yè)化裝置在湖南衡陽市氮肥廠投運到現(xiàn)在,安淳人經(jīng)過多次對技術(shù)的工業(yè)化適用性、工藝配套的節(jié)能性、工程設(shè)計的可行性及工藝優(yōu)化等方面進行了大量的工作,經(jīng)過了幾次大的技術(shù)提升,幾次大的完善性技術(shù)改造,創(chuàng)造了多種適應(yīng)于不同生產(chǎn)類型、不同生產(chǎn)廠家和不同生產(chǎn)條件的工業(yè)配套模式,極大地豐富了本技術(shù)的可適用性,也大大地節(jié)約了技術(shù)受讓廠家的工程投資,創(chuàng)造了更大的經(jīng)濟、社會效益及環(huán)保效益。到目前為止,雙甲工藝及提升技術(shù)——醇烴化工藝已經(jīng)在全國中、小合成氨企業(yè)推廣達40余家。已經(jīng)投用了的每一個廠家都有其工程設(shè)計及技術(shù)實施方法的獨特性,筆者作為技術(shù)開發(fā)者之一,長期進行本技術(shù)的推廣和配套工作,特撰文以總結(jié)之。
1 雙甲(醇烴化)工藝的基本原理
1.1 雙甲(醇烷化)工藝基本原理
雙甲工藝——甲醇化反應(yīng)串甲烷化反應(yīng),即以甲醇化反應(yīng)來脫除脫碳工段后的工藝氣中的CO+CO2,達到0.03%~0.3%,再以甲烷化反應(yīng)將此氣體精制到15×10-6以下,完成對合成氨原料氣的凈化精制。其基本方法是在合成氨原料氣的凈化精制中,在一定的壓力和有關(guān)工藝條件下,先以甲醇化反應(yīng)來凈化合成氨原料氣,將其中部分的CO+CO2和H2反應(yīng)生成甲醇產(chǎn)品,同時也使工藝氣體得到了凈化。這時原料氣中絕大部分的CO+CO2被脫除干凈。再將氣體送入甲烷化工序進行精制,精制后達到CO+CO2總量在(5~15)×10-6,最終獲得了可進入氨合成工序的合格原料氣。
反應(yīng)同樣以CO+CO2與H2作為原料,生成了CH4。但反應(yīng)主要目的是精制合成氨原料氣——將甲醇化后的只有很少量的CO+CO2進行脫除。為了減少精煉氣的放空量,我們要盡量使進入甲烷化中的CO+CO2少,這也是雙甲工藝中比較注重的工程技術(shù)問題。
1.2 雙甲工藝的升級技術(shù)醇烴化反應(yīng)基本原理
醇烴化反應(yīng)是為了降低原料氣中的H2耗量。因甲烷化反應(yīng)的反應(yīng)生成物全部為CH4氣體,這種惰性氣體要在合成工段放空,增加了合成工段的氣耗和電耗。我們創(chuàng)造了一種催化劑來取代甲烷化催化劑對工藝氣體進行精制,這種工藝我們稱之為醇烴化精制工藝。反應(yīng)是在精制反應(yīng)器內(nèi)的催化劑床中完成的,大部分氣體中的CO+CO2和H2進行了醇化反應(yīng),少量的氣體進行了烴化反應(yīng),生成了多元醇類和極少量烴類和水的混合物,達到以液態(tài)副產(chǎn)品輸出方式的目的,使合成工段的循環(huán)氣放空量基本不增加。這種副產(chǎn)品可進入甲醇精餾工段回收完多元醇類產(chǎn)品后再和甲醇精餾后的殘液一道作為燃料使用;蛑苯訉⒋紵N化液作為燃料使用。也就是說醇烴化反應(yīng)為大部分是液態(tài)的副產(chǎn)品輸出,而甲烷化反應(yīng)則是以氣態(tài)的副產(chǎn)品輸出的方式。
由于碳原子在分子中以多碳結(jié)構(gòu)存在,也就是說碳原子形成了“鏈”,這樣的分子結(jié)構(gòu)形態(tài)就可以減少H2的耗量。通過多次優(yōu)化,我們不斷改進醇烴化催化劑的配方,目前通過醇烴化精制生產(chǎn)出來的副產(chǎn)物主要成份為:水39%,甲醇33%,乙醇15%,其他多元醇13%。
由于是液態(tài)取樣,生成的甲烷及其他常溫下?lián)]發(fā)的二甲醚類等物質(zhì)未分析出來。采用這種催化劑,醇烴化的出口物質(zhì)大部分為醇類物質(zhì)。這些物質(zhì)是完全可以燃燒的,無毒,可以作為清潔燃料使用的。2 幾種典型的雙甲(醇烴化)工藝的工程設(shè)計模式
2.1 不同壓力級組合的設(shè)計模式
2.1.1 等壓力級的雙甲凈化工藝設(shè)計模式
雙甲工藝發(fā)明之初,1992投產(chǎn)的湖南衡陽氮肥廠是世界上第一套雙甲工藝,當(dāng)時國內(nèi)的常溫精脫硫技術(shù)尚未進入工業(yè)化,我們采用了甲醇塔內(nèi)置高溫氧化鋅精脫硫劑的方式來進行精脫硫,將高溫氧化鋅放置在甲醇化合成塔催化劑的上部。由于當(dāng)時甲醇市場較好,我們工程設(shè)計中采用了雙塔可“串聯(lián)”可“并聯(lián)”運行的甲醇化工序設(shè)計方式,生產(chǎn)中將變換出口氣的CO提高到了5%以上,得到了甲醇產(chǎn)量較高,甲烷化精制效果也好的結(jié)果。
后來再經(jīng)過優(yōu)化設(shè)計,也有了湖南郴州地區(qū)橋口氮肥廠、山西豐喜集團臨猗分公司、湖南湘陰氮肥廠、吉林梅河口化肥廠等廠都采用了這種在12.5~15MPa級等壓力級條件下的雙甲工藝模式。
本流程比較適應(yīng)于原來廠家已經(jīng)有這一壓力級的聯(lián)醇崗位,也適應(yīng)于由銅洗改造成雙甲工藝的單位?梢栽趬嚎s機“五出”或“六出”總管上由原來進入銅洗工段的管道上接雙甲工藝,不需要再設(shè)置壓縮機出口總管,也適應(yīng)于以凈化精制合成氨原料氣為主的單位。況且,目前的銅系甲醇催化劑已經(jīng)能在這個壓力下獲得很高的轉(zhuǎn)化率,我們認為再提高壓力也不會使甲醇化的轉(zhuǎn)化率提高很多;诖,如果是以凈化為目的而設(shè)雙甲工藝的廠家,我們首先推薦這種模式來完成工程設(shè)計,后來如山西晉豐集團高平化肥廠、山西晉豐聞喜化肥廠、江蘇華爾潤化工有限公司、山東德齊龍化工有限公司等廠均采用了這種配置方式。
這種配置工藝的最大優(yōu)點是甲醇化后的氣體不要經(jīng)過壓縮,減少了壓縮油污染的氣體對甲烷化或醇烴化催化劑的影響;其二,醇化系統(tǒng)設(shè)在一個壓力級便于兩工序循環(huán)機的共用,也便于操作管理;其三,可以利用甲醇化的反應(yīng)熱來加熱醇烴化或甲烷化的入爐氣體;其四,可利用原銅洗的高壓設(shè)備改作甲烷化或醇烴化設(shè)備。
另一個要注意的是由于甲烷化催化劑對甲醇和二甲醚等類物質(zhì)比較“敏感”,會影響其反應(yīng)活性,因此,如果是采用甲烷化反應(yīng)來進行精制(醇烷化工藝),則必須要考慮在甲醇化后設(shè)一個洗醇崗位,以軟水來洗凈尾氣中的微量甲醇和二甲醚,達到保護甲烷化催化劑之目的。 這種配置的典型流程圖1。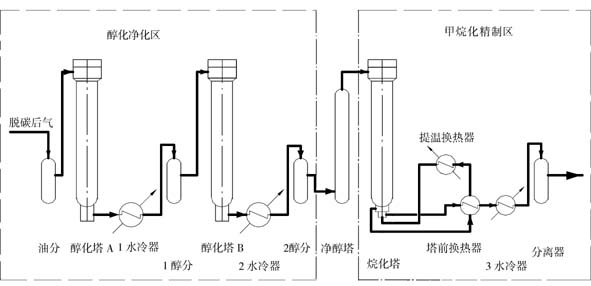
圖1 醇化或烷化等壓力下的雙甲工藝流程
2.1.2 與氨合成系統(tǒng)等壓力級的雙甲凈化工藝設(shè)計模式
當(dāng)建設(shè)方有部分高壓設(shè)備可供利用,而雙甲工藝又是以凈化為目的運行方式時,我們也考慮雙甲工段和氨合成壓力等壓的流程進行系統(tǒng)設(shè)計。
這種方式特別適應(yīng)于氨合成系統(tǒng)改造和凈化精制改造同時進行的工程,如我公司在2001年為邯鄲鋼鐵集團公司化肥廠等廠設(shè)計的系統(tǒng)。當(dāng)時,廠家正要進行DN1600氨合成系統(tǒng)改造,原來的氨合成系統(tǒng)有很多設(shè)備可供利用,我們?yōu)榇嗽O(shè)計了一套醇化系統(tǒng)和甲烷化系統(tǒng)均為32MPa的雙甲凈化精制系統(tǒng),醇化和烷化運行壓力均為32MPa,這個壓力和氨合成系統(tǒng)壓力一樣。裝置運行近6年了,目前運行狀況良好。后來相繼有部分廠家也運用了本設(shè)計方式進行系統(tǒng)配套。
這種設(shè)計方式的優(yōu)點之一是可利用原來氨合成的舊設(shè)備,不需要將原設(shè)備以降低使用壓力的方式進行使用,可提高催化劑的利用率,也可以提高甲醇化的能力;優(yōu)點之二,是在高壓下運行,催化劑使用“空速”可適當(dāng)提高,系統(tǒng)熱利用也高,熱損失相對也較小,還可以提高一些反應(yīng)速度;優(yōu)點之三,是經(jīng)過雙甲工藝后的氣體不需要再經(jīng)過壓縮機來增壓,減少了氣體被壓縮機油污染的機會,更大程度地保護了氨合成催化劑。缺點之一,當(dāng)產(chǎn)醇量較高時,將會使使制醇氣體壓縮功耗比在中低壓下的壓縮功耗增加,經(jīng)過計算,生產(chǎn)1噸甲醇的原料氣,由12.5MPa壓力級壓縮到26MPa壓力級,壓縮機將增加電耗53 kW·h;缺點之二,不能認為提高醇化反應(yīng)壓力可以較大幅度地提高甲醇化的轉(zhuǎn)化率,也就是說,10MPa以上的甲醇化反應(yīng),利用目前銅系催化劑,轉(zhuǎn)化率提高也相當(dāng)有限了,相反還會增加甲醇反應(yīng)的副反應(yīng),使產(chǎn)品甲醇的品質(zhì)受到影響。
本工藝的基本流程與圖1一樣。
2.1.3 在12.5~32MPa壓力級任一壓力下等壓下的醇烴化凈化精制工藝
按2.1.1和2.1.2的配置方式設(shè)計的雙甲系統(tǒng),同樣適用于醇烴化工藝。我們在2000年后,為了提高雙甲工藝的技術(shù)水平,減少能量消耗,提高氣體利用率,創(chuàng)造了醇烴化工藝。工藝先期是采用醇化后串烴化的方法,這種烴化反應(yīng)主要是利用一種烴化催化劑來實現(xiàn)。烴化產(chǎn)品由于反應(yīng)選擇性強,要求溫度控制在一定的范圍。為了更有其工程可行性或?qū)嵱眯,后期又?chuàng)造了更加方便的甲醇化再串醇烴化的工藝方式。也就是說,在原來裝甲烷化催化劑的反應(yīng)爐內(nèi),換裝上醇烴化催化劑(這一種催化劑同時完成醇化和部分烴化反應(yīng)的催化劑,故稱之為醇烴化)。這樣即達到了盡量多產(chǎn)有用的醇類產(chǎn)品的目的,也可以使深度精制達到合成氣的要求。
醇烴化技術(shù)基本原理是利用甲醇工序?qū)铣砂痹蠚膺M行醇化反應(yīng)并副產(chǎn)甲醇產(chǎn)品,同時對氣體中的CO+CO2進行初步脫除(甲醇化),再利用醇烴化工序的醇烴化反應(yīng)進行合成氨原料氣的進一步精制,并副產(chǎn)醇類物和烴類物的混合物等有用的常溫下可分離的物質(zhì)。工藝的第一步是將CO+CO2首先轉(zhuǎn)化為CH3OH,使CO+CO2 下降至0.03~0.3%;第二步是將少量CO+CO2在醇烴化反應(yīng)器內(nèi)轉(zhuǎn)化為低碳烴類物、低碳醇類物、甲醇和少量甲烷,最后使精制氣中的CO+CO2小于10×10-6,再進入氨的合成工序。這種工程設(shè)計可取消醇化后的凈醇處理工作,簡化了流程,降低了消耗量。
我公司在山東德齊化工有限公司的兩套“1830工程”、天脊集團晉城化工公司等廠均采用了這樣的設(shè)計方式。流程見圖2。
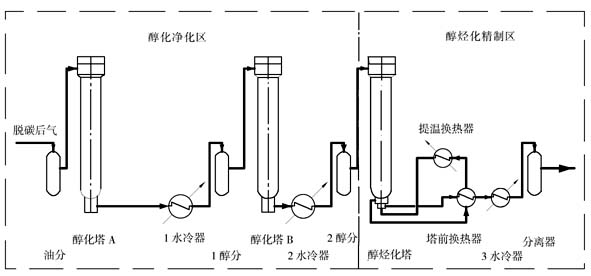
圖2 甲醇化和醇烴化等壓力下的醇烴化工藝流程
2.1.4 不等壓力級的雙甲(醇烴化)設(shè)計模式
醇化工序或甲烷化(醇烴化)工序可以在一個壓力級下進行,但也可以按工廠實際情況進行分級分不同的壓力下進行。如我公司為河南心連心、湖南岳陽、湖南衡陽、瑞星化工有限公司、江蘇新沂恒盛化工有限公司、河南心連心化工有限公司等多套改造工程的醇烴化工藝,為江蘇華昌化工有限公司、山東德齊龍化工有限公司的高產(chǎn)量甲醇聯(lián)醇烴化工藝均采用了不同型式的不同工序的不等壓的設(shè)計方式,這些廠家均收到了很好的效果。
還有一種方式是將一級和二級甲醇化反應(yīng)放在一個壓力級,將甲烷化(或醇烴化)放置在另一個壓力級。流程中只有一個區(qū)別是當(dāng)采用甲烷化進行精制時,必須在甲醇化后設(shè)一個醇洗工序,用以去除相應(yīng)溫度下分離不出來的甲醇及二甲醚。由于甲醇化后的氣體要再次進入壓縮工序,也要采用除油處理方式來保證醇烴化或甲烷化的催化劑安全。典型的流程見圖3。
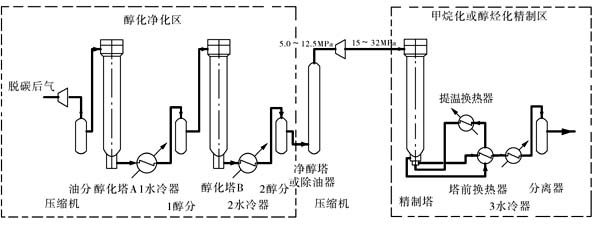
圖3 二級醇化等壓力甲烷化或醇烴化不等壓力的流程
圖3所示的這種流程的優(yōu)點是,二級甲醇化均在同一個壓力級進行反應(yīng),已經(jīng)有聯(lián)醇及聯(lián)醇設(shè)備的廠家改成雙甲工藝時,可不用費較大的工程量。
這種流程的甲醇產(chǎn)量可以做得較大,二級甲醇化的碳CO+CO2的轉(zhuǎn)化率也可以達到很高(二級甲醇化后的CO+CO2可達到0.03%),二級甲醇可共用循環(huán)機,并且甲醇化塔“可串可并”,可以一塔操作,一塔更換催化劑和升溫還原,當(dāng)甲醇產(chǎn)量較低時,也可以一個塔生產(chǎn)、一個塔備用,調(diào)配十分方便。
保證將較好的催化劑活性的塔設(shè)在二級甲醇化,保證了二級甲醇化對原料氣的深度凈化的要求。
甲烷化或醇烴化如果設(shè)在更高一級的壓力級,可使用退下來的舊的氨合成系統(tǒng)設(shè)備,使甲烷化催化劑或醇烴化催化劑使用量變少,精制度提高,也有利于從合成系統(tǒng)取熱來供甲烷化爐或醇烴化爐。
這種流程的缺點是流程相對較長,在甲醇化和甲烷化中要設(shè)除油或凈醇工序,多設(shè)的各級不同的壓力,也給生產(chǎn)管理和操作帶來了一定不便。
這種流程的缺點是流程相對較長,在甲醇化和甲烷化中要設(shè)除油或凈醇工序,多設(shè)的各級不同的壓力,也給生產(chǎn)管理和操作帶來了一定不便。
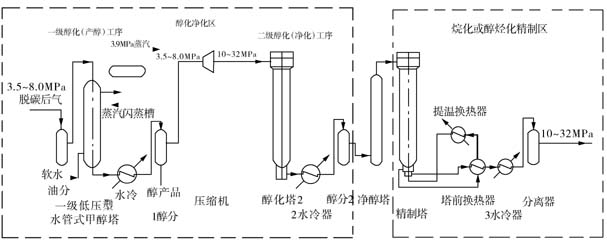
圖4 二個醇化塔的操作壓力不相同,精制塔與第二級醇化等壓力的流程
圖4所示流程是最近我們在山東德齊龍化工有限公司研制投用成功的一種全新的、產(chǎn)醇量大、凈化精制度高,調(diào)節(jié)十分方便的流程。
這種流程的優(yōu)點是產(chǎn)醇量可以做到很大,生產(chǎn)1噸甲醇可副產(chǎn)高品位蒸汽(蒸汽壓力3.9 MPa)1.4~1.5t,只要將產(chǎn)生的蒸汽在其他崗位進行過熱后,就可以進行差壓發(fā)電,發(fā)電后的背壓蒸汽還可作工藝用汽,可獲得很好的經(jīng)濟效益。
第一級甲醇在低壓力下完成,有效地節(jié)約了壓縮功耗。這也是非常符合我們提出的產(chǎn)醇在低壓下進行、凈化精制在高壓下進行的工藝理念。
這種流程的另一個優(yōu)點是第一級甲醇化塔產(chǎn)醇量無論多大,因是采用3.9MPa壓力級的飽和水來調(diào)節(jié)催化劑床層的溫度,比傳統(tǒng)的氣氣換熱的反應(yīng)器調(diào)溫方便,操作安全性強。但這種流程不太適應(yīng)于產(chǎn)醇量小時的工廠,如果用這種流程,第一級醇化塔的投資較大,流程也較長。
當(dāng)然,也可以將第一級甲醇塔設(shè)為普通的氣氣換熱方式的反應(yīng)器,雖然回收的蒸汽量較少,蒸汽品位較低(0.2MPa左右),但卻比較適應(yīng)于目前很多廠家已經(jīng)有這一級壓力的聯(lián)醇系統(tǒng),也有相當(dāng)成熟的操作經(jīng)驗。但我們認為,從產(chǎn)醇塔的反應(yīng)機理上來看,不主張大量生產(chǎn)甲醇的塔用冷激式降溫的方式來制造反應(yīng)器,這樣對熱回收、對降低循環(huán)量、對保護甲醇催化劑和提高產(chǎn)品甲醇的品質(zhì)等方面均沒有好處。
2.1.5 不同壓力級分配的雙甲工程設(shè)計小結(jié)
安淳公司的設(shè)計者們從工廠的實際出發(fā),采用我公司的專利技術(shù),按照雙甲(醇烴化)工藝的特點,十多年來為用戶設(shè)計了近40多套凈化精制工藝,曾經(jīng)運用了各工序的多種壓力級配置的設(shè)計方式。有“等壓”的雙甲流程、也有“等高壓”的雙甲流程、“非等壓”的雙甲流程和甲醇不等壓,甲醇與醇烴化也不等壓力級的“非等壓”流程。至于各工序的壓力級如何配置,要依照催化劑和反應(yīng)條件進行流程配置。換言之,無論采用何種壓力級進行工序配置,目的要使反應(yīng)器和催化劑發(fā)揮最大效益、要使系統(tǒng)能力達最大化、安全化、要使系統(tǒng)流程最為簡化,最終達到最好的綜合效益。
2.2 不同產(chǎn)出物的工程設(shè)計方式
雙甲工藝有二個或三個反應(yīng)器,每一個反應(yīng)器均要在有催化劑條件下進行反應(yīng),主要原料為CO+CO2和H2。而這些原料是組成碳氫化合物的基本原子,如果我們運用不同的反應(yīng)條件和相應(yīng)的催化劑,理論上來講,可以得到多種有機反合物。
目前最為成熟的方式可以得到甲醇和二甲醚及甲烷或多元醇烴類物質(zhì)。如果進一步研究也可以得到汽油的替代物,我們在雙甲工藝中采用了不同的催化劑,也創(chuàng)造了幾種產(chǎn)品生成物的設(shè)計方式。
2.2.1 生產(chǎn)醇醚燃料的雙甲工藝
1996年在湖南湘陰氮肥廠的雙甲工藝改造中,在甲醇化爐內(nèi)放入我公司研制的醇醚催化劑,生產(chǎn)出了醇醚混合物的副產(chǎn)物。并用這種物質(zhì)進行了作民用醇醚燃料的推廣工作,取得了可喜的成果。也為一步法合成二甲醚進行了前瞻性的工作,目前正在進行“一步法”生產(chǎn)二甲醚的深入研究工作。
如果再采用相配套的精餾方式,可以同時得到甲醇和二甲醚兩種產(chǎn)品供應(yīng)市場。這種工藝方式為甲醇類廠家生產(chǎn)二甲醚提供了經(jīng)驗,也為利用本系統(tǒng)流程生產(chǎn)其他碳一化工類產(chǎn)品提供了經(jīng)驗。工藝流程見圖5。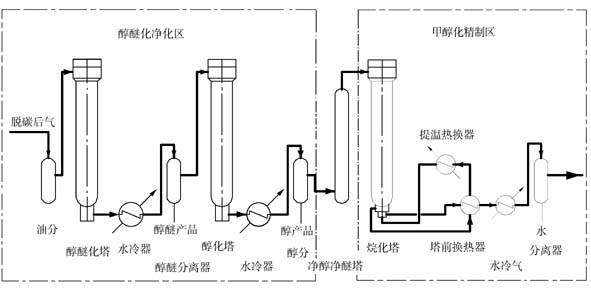
圖5 甲基化產(chǎn)二甲醇及醇類混合物的雙甲凈化精制流程
這種配置方式的優(yōu)點是為小型化肥企業(yè),特別是產(chǎn)碳銨的企業(yè)在肥料銷售淡季可提供甲醇或醇醚原料產(chǎn)品選擇。
2.2.2 將甲烷化爐內(nèi)催化劑換成醇烴化催化劑將得到優(yōu)質(zhì)燃料的精制工藝
如圖5的流程一樣,如果將甲烷化塔內(nèi)的催化劑換成醇烴化催化劑,或?qū)⑵浯呋瘎┡浞絻?yōu)化,或生產(chǎn)出多元醇產(chǎn)品的優(yōu)質(zhì)燃料,將其中的甲醇等類物質(zhì)精餾出來,可更進一步得到甲醇產(chǎn)品。也就是說,甲烷化精制生成的副產(chǎn)物為氣態(tài)的甲烷,這種甲烷只有隨氣體進入氨合成工段以放空的形式排掉;而醇烴化精制生產(chǎn)的副產(chǎn)品絕大部分為液態(tài)的多元醇類產(chǎn)品,這種產(chǎn)品可用以代替液化氣作為燃料產(chǎn)品出售,因而它有更高的經(jīng)濟和環(huán)保效益。
這種產(chǎn)出物也可作為燃料進入鍋爐或造氣系統(tǒng)燒掉。還可以將液體送入甲醇的精餾系統(tǒng),回收其中的33%的甲醇后,其余物質(zhì)隨甲醇精餾的殘液送入鍋爐或造氣系統(tǒng)燒掉。
這種產(chǎn)品工藝改進的方式直接帶來了原料氣中的H2消耗量比同樣條件下甲烷化反應(yīng)的H2消耗下降近24%,也使合成放空量減少80%。
這種方式是基于我公司創(chuàng)造的醇烴化催化劑技術(shù),在一定條件下設(shè)置工藝,主要目的是減少原料氣消耗。
2.3 采用不同的醇氨比設(shè)計的雙甲工藝
安淳公司在上世紀90年代初期,已經(jīng)申請了一個可調(diào)醇氨比的雙甲工藝的技術(shù)發(fā)明專利技術(shù),它的核心內(nèi)容是運用兩級甲醇系統(tǒng)的工程設(shè)計方式,第一級甲醇系統(tǒng)著眼于多產(chǎn)甲醇產(chǎn)品,第二級甲醇系統(tǒng)立足于對原料氣進行深度凈化。這樣整個工序運行可以十分安全地應(yīng)付甲醇產(chǎn)量的變化或氣量的變化,催化劑在初期、中期和未期均能十分方便地調(diào)節(jié)系統(tǒng),達到系統(tǒng)始終處于高效節(jié)能的運行狀態(tài)。
我們的工程實踐中,有的單位醇氨比達到了1:2(湖南衡陽市氮肥廠,山東德齊龍化工有限公司)或更高,而以凈化為目的的廠家醇氨比僅只有1:20(山東德齊龍化工有限公司、邯鋼集團化肥廠、河南心連心化工有限公司等廠),這些廠家系統(tǒng)運行安全十分可靠。進入烷化或醇烴化的氣體中的CO+CO2量也在0.3%以下,最小的可達0.03%。當(dāng)然,甲烷化或醇烴化的外供熱也相應(yīng)增加了一些。
2.4 精制工序的不同的外供熱的設(shè)計方式
通過醇化串醇烴化或甲烷化各反應(yīng)器的熱量衡算及工程實際證明,采用甲烷化反應(yīng)方式作為精制時,要達到甲烷化爐內(nèi)的反應(yīng)熱量平衡,通常的控制指標是讓進甲烷化爐內(nèi)的CO+CO2量大于0.7%;進入醇烴化爐內(nèi)的CO+CO2量要大于0.5%(因醇烴化反應(yīng)比甲烷化反應(yīng)的溫度低)。
如果采用這樣的成份入甲烷化爐內(nèi),將會有較多的CH4生成,也會增加原料氣的H2的消耗量。造成合成工段的放空量增加;如果進入醇烴化工段,也會使副產(chǎn)的多元醇類產(chǎn)品增加,造成精餾的負荷增加,工程上要盡量降低這個指標,將有效的氣體多生產(chǎn)甲醇類產(chǎn)品。
我們一般是將進入醇烴化或甲烷化的CO+CO2這個值定為0.03%~0.3%,這樣勢必在精制工段要采用外供一部分熱量來保證反應(yīng)器運行正常。當(dāng)然,如果生產(chǎn)的是人造汽油產(chǎn)品或生產(chǎn)的是暢銷的民用燃料產(chǎn)品,我們會要求產(chǎn)品產(chǎn)量愈高愈好,那時,工藝上也將會有個較大的調(diào)整。
以年產(chǎn)100kt氨副產(chǎn)31.3kt粗醇為例:變換氣中CO 4.31%,原料氣中CO 5.95%、CO2 0.31%,醇后氣CO、CO2含量與補充熱(以電功率計算)的關(guān)系如表1。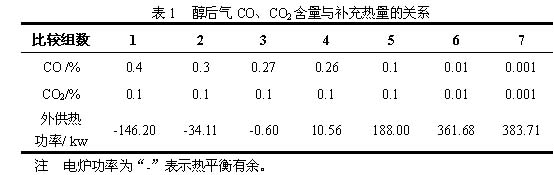
由表1看出,不計熱的損失,也不考慮有水冷卻器部分的熱量損失的條件下,只考慮反應(yīng)平衡的條件下,CO+CO2為0.37%時(3組)不需外供熱,但CO+CO2下降為0.36%時(4組),需外供熱10.56kw;CO+CO2降至0.2%時(5組),外供熱增加188.00kw,即成份(CO+CO2)下降44%,外供熱增加16.8倍,隨著CO+CO2的降低,外供熱隨之增加直至CO+CO2為0.002%時,外供熱(電)達到383.71kw。
一般來說,要維持低組分下的反應(yīng)熱平衡,盡量要降低進入水冷卻器的氣體溫度,也要提高催化劑活性,提高較化率,更不能開用循環(huán)機,開了循環(huán)機將會使系統(tǒng)的熱損失更大。也要盡量降低系統(tǒng)的熱損失,才能夠以最少的外供熱量來實現(xiàn)熱平衡反應(yīng)。當(dāng)然工程實際中要考慮多種因素,因而要充分留有余量來設(shè)計系統(tǒng)。
雙甲工藝的工程設(shè)計中,我們采用多種方式向系統(tǒng)補熱。
2.4.1 用發(fā)電蒸汽取熱的方式
這種方式是采用一個蒸汽加熱器來加熱甲烷化或醇烴化爐進口氣體,過熱蒸汽的溫度要在260℃以上,工藝只需將精制塔進口氣的溫度由190~200℃加熱到210~220℃(采用醇烴化精制時入口溫度,當(dāng)用甲烷化時,溫度至少要高20℃以上)。
我們在河南心連心化工有限公司、湖南岳陽天潤化工有限公司等廠均采用這種方式來補充熱量,利用原合成系統(tǒng)的舊廢熱鍋爐來實現(xiàn)本工藝。加熱的流程見圖6。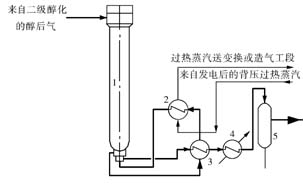
圖6 利用過熱蒸汽加熱精制反應(yīng)器流程
1—醇烴化或烷化塔;2—提溫換熱器;3—塔前換熱器;4—水冷器;5—水或醇烴化合物分離器
這種流程的優(yōu)點是間接加熱氣體,不需要設(shè)置一個內(nèi)外均是耐高溫和能承受高壓的氣氣換熱器。這種間接加熱方法安全可靠;可以利用舊的合成塔出口廢鍋來改造用之。這種方式必須有過熱蒸汽的來源,換熱過程是取蒸汽的顯熱,沒有一定的蒸汽流量,也不會使加熱過程順利。
2.4.2 利用變換系統(tǒng)的熱量來加熱精制塔進口氣
當(dāng)變換為“中變串低變”或“全中變”的流程時,可利用中溫變換爐出口的310~400℃的反應(yīng)出口氣,利用傳熱介質(zhì)來間接加熱甲烷化或醇烴化爐的進口氣體。這種流程可在變換爐出口設(shè)一個U型管換熱器,管外走變換氣,管內(nèi)用走傳熱介質(zhì);同時也在醇烴化或甲烷化爐的進口設(shè)一個U型管換熱器,管內(nèi)走高壓入口氣,管外走熱介質(zhì),利用熱介質(zhì)的流量來調(diào)節(jié)加熱入爐氣。
這種流程相對簡單,不是用氣氣直接換熱的高溫高壓換熱器來加熱,從而減少了換熱器泄漏造成氨合成塔內(nèi)的催化劑“中毒”危害。但使用這種流程必須要有一個中溫變換工序,如果是采用“全低變”的變換工藝,因反應(yīng)氣的溫度與甲醇化和甲烷化的反應(yīng)溫度相近,無法用此方法來換熱。
2.4.3 利用合成工段的出口氣熱量來加熱精制塔進口氣
這種加熱的方式我們1996年就在有關(guān)文章中提出過,也進行過詳細的流程考慮。由于此種方式要增加一個抗氫腐蝕、且能耐高壓的設(shè)備于合成塔的二出口入廢熱鍋爐的管線中,而換熱采用的是氣氣直接換熱的方式,要考慮到很多安全性等問題。為了使內(nèi)件壓差不至于太大而造成內(nèi)件設(shè)計更為困難,最好是將合成壓力和精制系統(tǒng)壓力設(shè)計成一個壓力級,從而也限制了使用范圍,基于此,我們更多地是考慮用其他方式來取熱用于精制塔。
這種取熱方式的優(yōu)點是,可以長期利用合成系統(tǒng)的高溫反應(yīng)熱,采用高溫反應(yīng)氣來直接加熱較低溫的未精制氣的方式,采用直接的氣氣換熱方式。只要把換熱器設(shè)計好,系統(tǒng)開停車安全性考慮周到,各管線和閥門用材料考慮周到,基本上是可以穩(wěn)定地操作運行。
但這種方式的流程很復(fù)雜,要用很多抗氫蝕、耐高溫的特種管材。為了有利于節(jié)約有關(guān)特種材料的管線,要求氨合成系統(tǒng)與凈化精制系統(tǒng)位置相距不遠,也要求氨合成工序和精制塔的反應(yīng)壓力在同一個壓力級。
運用這種流程,有多個相關(guān)聯(lián)的換熱器,具體是合成的塔外換熱器、精制部分的塔外換熱器、加上應(yīng)設(shè)的這個跨工序的提溫換熱器,假若這個運行條件很苛刻的提溫加熱器一旦泄漏,哪怕是一點小的泄漏,將會造成未精制的含CO+CO2在0.03%~0.3%的原料氣進入氨合成工段,造成進入氨合成塔的氣體中的微量增高,造成催化劑中毒,氨合成系統(tǒng)的熱交換器的熱負荷和醇化部分塔外換熱器的熱負荷也會相應(yīng)變化。
(流程圖略)
同樣是在合成塔部分取熱,我們也發(fā)明了一種間接換熱方式——將耐熱介質(zhì)加熱后,再通過另外的間接加熱器,將熱量傳熱給精制塔進口氣的方式。這種方式在我公司設(shè)計的河南晉開的醇烴化工程、貴州開磷集團劍江化肥有限公司的醇烴化工程設(shè)計被采用。
2.4.4 取造氣工段或鍋爐工段高溫?zé)岬姆绞?/DIV>
在合成氨廠,只要有穩(wěn)定的溫度在300℃以上的熱源就可以來加熱精制塔進口氣體,我們在造氣工段的吹風(fēng)氣回收鍋爐內(nèi),或在鍋爐工段的省煤器前設(shè)一個加熱器,用間接換熱的辦法,同樣利用傳熱介質(zhì)來加熱精制塔入口氣,這也是一種好的方法。但設(shè)備設(shè)計可靠性研究及工段取熱的方便性將被視為工程設(shè)計的重點。這些取熱方式將視廠家的具體情況因地制宜而選之。
2.4.5 利用適當(dāng)控制精制塔入口氣體成份的方式輔助用電爐直接加熱
通過表1可知,當(dāng)氣體中的CO+CO2量達到一定值時,可使外供熱量減少或不需外供熱,而我們?yōu)榱私档虷2的消耗,盡量要使進入精制塔內(nèi)氣體的CO+CO2量少一些,這就有一個“度”的把握問題,一個優(yōu)化操作控制的問題。
我們不主張將這個指標降得過低,一般來說,當(dāng)進入精制塔的CO+CO2量約0.3%就可以了,這樣加入的熱量也不多,操作也方便。
表2中列出了醇后氣成份與氣體消耗的關(guān)系,通過表2可知,在CO+CO2為0.3%左右時的氣體消耗量增加并不很大。綜合表1數(shù)據(jù)分析,只要控制熱量損失小,進水冷卻器的溫度控制低一些,也有可能達到系統(tǒng)的熱量反應(yīng)平衡。
我們設(shè)計的正在使用的雙甲工藝系統(tǒng)中,很多廠家都采用這種帶一定的補充電爐熱的甲烷化或醇烴化爐的操作法,只要控制得法,也達到了安全高效的運行效果。一般來說,每噸總氨的補充耗量均小于10kW·h,也不破壞其他工段的熱平衡。
這種方式操作簡便、投資小、綜合效益好。我們第一套雙甲工藝在湖南衡陽氮肥廠投產(chǎn)至今已經(jīng)成功運行了15年,先期為醇烷化工藝,后改成醇烴化工藝,一直采用外供電補熱的方式,安全運行這么多年,他們認為采用醇烴化比醇烷化的外供電量消耗小得多。因此,采用醇烴化精制不但可以減少外供熱量,減少原料氣中的H2耗量,同時還可以得到副產(chǎn)品中的醇,創(chuàng)造比烷化精制更好的效益。
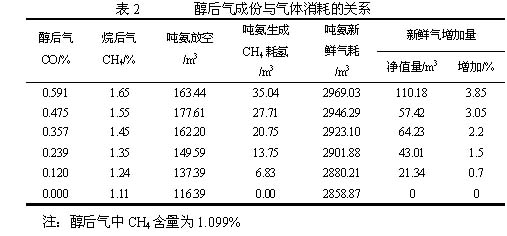
2.4.6 各種取熱方式總結(jié)
在雙甲工藝的工程運用中,我們?yōu)榱私档驮蠚庵械腍2消耗,人為地要將甲醇化后的CO+CO2量控制小一點,讓其多在甲醇化系統(tǒng)產(chǎn)甲醇產(chǎn)品。一般來說控制在0.03%~0.3%,這樣盡量讓有效的氣體變成有用的產(chǎn)品,而不要變成“廢物”。
但如果甲醇化后的氣體CO+CO2指標過低,外供熱就會增大,這個指標,醇烴化反應(yīng)也不能達到“全自熱”,更何況醇烷化工藝。因此,必須要采用有效的外供熱來實現(xiàn)這一目的。大多數(shù)控制方式是將進入醇烴化或甲烷化爐的指標適當(dāng)化,不一味追求太低的指標,也采用因地制宜的外供熱方式,具體供熱方式要視方便化程度、投資情況及整個合成氨工藝配備的條件而定,要算經(jīng)濟帳、環(huán)保帳。最簡單、最經(jīng)濟的取熱方式應(yīng)當(dāng)是我們所共同追求的。
甲烷化或醇烴化要達到“全自熱”,也就是說精制塔全部靠自身的反應(yīng)熱來維持反應(yīng)平衡,工程中必有一定的入口氣反應(yīng)物組分,才能有一定的能夠支付熱損失和水冷器降溫帶走的熱量,否則,不論你的換熱器做得多好,要達到自熱是不可能的。如果要向外工段“取熱”,就談不上“全自熱”。
上面列舉的各種“取熱”方式,我公司均有實施的先例,或正在實施,總的來說,我們認為因地制宜的設(shè)計是最適合使用廠家的方式,應(yīng)該是用戶能接受、能給用戶帶來更好效益的方式。也就是說,工程問題是最具實踐性的問題,只有不斷結(jié)合不同廠家的具體情況進行工藝及設(shè)備優(yōu)化設(shè)計,才能使一個好的工藝及技術(shù)達到應(yīng)有的水平。
3 結(jié) 語
醇烴化工藝是合成氨的具有革命性的成果,它可使原料氣CO+CO2降到(5~15)×10-6。醇烴化工藝除了精制氣體功能之外,還利用變換后的CO、脫碳后的CO2副產(chǎn)粗甲醇或醇醚混合物,還可利用醇烴化催化劑生產(chǎn)多優(yōu)質(zhì)的民用燃料,生產(chǎn)中完全可實現(xiàn)“零污染、零排放”。
本技術(shù)由發(fā)明之初的只有一到兩種副產(chǎn)品和單一的流程設(shè)置方式,發(fā)展到現(xiàn)在有各種流程配置方式和能夠生產(chǎn)多種副產(chǎn)品的技術(shù)。工藝成功地進行了兩次技術(shù)突破性地“升級”,目前全國中、小合成氨行業(yè)有近40家企業(yè)使用了這個技術(shù),合成氨凈化精制能力由40kt/a總氨到400kt/a總氨均有技術(shù)運用,無論是雙甲凈化精制工藝還是醇烴化凈化精制工藝均收到了十分顯著的環(huán)保效益和經(jīng)濟效益。
本工藝被列為國家級重點科技成果推廣項目計劃,列為我國合成氨行業(yè)的環(huán)保節(jié)能首先技術(shù)項目,獲得了國家科技進步二等獎。
安淳公司在設(shè)計雙甲工藝流程及選擇設(shè)計中,運用了因地制宜的設(shè)計方法,不斷優(yōu)化系統(tǒng),創(chuàng)造了多種工藝的配置和設(shè)計模式,可供同行業(yè)人士借鑒。無論在二級甲醇系統(tǒng)的壓力級的選擇上,各工序壓力級的組合上、多種熱利用方式的配備上、各工序進出口氣的成份控制上,還是在采用烷化工藝或醇烴化工藝的精制方法選擇上,都進行了深入的研究和創(chuàng)造了工程實例。
為了更進一步將醇烴化工藝推向更節(jié)能、更適用的技術(shù)高度,下一步將重點放在工藝配套的催化劑研究上,使雙甲工藝可以生產(chǎn)醇、醚或烯烴類基礎(chǔ)化工產(chǎn)品,也能夠生產(chǎn)汽油的替代品——人造汽油。我們期待著和國內(nèi)外有關(guān)同行合作,為我國的合成氨工業(yè)和能源工業(yè)創(chuàng)造更多的技術(shù)及實用工藝,為凈化籃天,創(chuàng)造好的經(jīng)濟效益而更多地工作。
元豐資訊:
氮肥與甲醇技術(shù)網(wǎng)
尿素網(wǎng)
造氣網(wǎng)
二甲醚網(wǎng)
尿素世界網(wǎng) (英文版)
產(chǎn)品技術(shù)庫
VIP商務(wù)俱樂部
化工論壇
QQ群大聯(lián)盟
地址:成都市青白江區(qū)怡湖芳鄰18棟8號 電話:028-83667786,83667576,89309098 傳真:028-83667578