1 醇烴化工藝開發(fā)簡況
合成氨原料氣醇烴化凈化精制工藝是雙甲工藝的升級技術(shù)。雙甲工藝是湖南安淳高新技術(shù)有限公司開發(fā)成功的原創(chuàng)型技術(shù),該技術(shù)于1990年提出,1991年進(jìn)行工業(yè)化,1992年9月第一套工業(yè)化裝置在湖南衡陽市氮肥廠投產(chǎn)成功,在國際上最早提出,最先進(jìn)行工業(yè)化生產(chǎn)。1993年4月獲國家發(fā)明專利,相繼又申請了可調(diào)節(jié)氨醇比的醇烴化專利技術(shù),美、英等權(quán)威化學(xué)文摘均作了報道。1994年元月通過化工部科技鑒定,1994年6月國家科委將該項目列入《國家重大科技成果推廣計劃》項目。第一套裝置至今已正常運行15年,目前這個示范廠的凈化精制能力上升到了總氨80kt/a,副產(chǎn)10kt/a甲醇,工藝投用以來,取得了很好的經(jīng)濟(jì)和社會效益。目前,推廣的工藝最大合成氨能力達(dá)400kt/a,在全國中、小合成氨廠推廣達(dá)35家之多。湖南郴州橋口氮肥廠的雙甲工藝被評為國家優(yōu)秀創(chuàng)新工程,雙甲工藝評為1995年度原化學(xué)工業(yè)部十二大重大科技成果之一,2000年被授予湖南省科技進(jìn)步一等獎,給予重點推廣。2003年醇烴化工藝獲得國家科技進(jìn)步二等獎。
此工藝開發(fā)和發(fā)展可分為三個階段,歷時近十五年的開發(fā)創(chuàng)新和竭力推廣,有著超乎尋常的辛勞,可謂“十年磨一劍”。
技術(shù)發(fā)展的第一階段——確認(rèn)了國產(chǎn)甲烷化催化劑在高壓條件下的運行條件。技術(shù)發(fā)展之初,當(dāng)有雙甲凈化工藝這個創(chuàng)意時,國內(nèi)的很多廠家已經(jīng)有了聯(lián)醇工段,一般為聯(lián)醇后再串銅洗進(jìn)行凈化精制,由于聯(lián)醇出口CO和CO2的指標(biāo)與傳統(tǒng)的甲烷化進(jìn)口氣體成分指標(biāo)不一樣,且壓力等級也不一樣,要將銅洗去掉用甲烷化來替代,必須首先解決進(jìn)甲烷化爐的進(jìn)口氣體的氣體成份問題——一定要使醇后氣中CO+CO2總量不超過0.7%,且越低越有利于提高氣體的利用率和降低氣體的消耗。
另外要使甲烷化催化劑能在甲醇之后的壓力級內(nèi)運行必須有一套可行的工藝條件及設(shè)備等來保證。而當(dāng)時,國際、國內(nèi)傳統(tǒng)鎳基甲烷化催化劑的使用壓力均在0.3MPa,而當(dāng)時甲醇催化劑活性壓力為13MPa,按工藝布置,甲烷化只能放置在甲醇后,因此,必須要找出甲烷化催化劑在高壓下的工況條件。我公司通過改變工藝條件、流程及設(shè)備結(jié)構(gòu),進(jìn)行了大量的實驗,模索出了一整套甲烷化催化劑在高壓條件下的運行條件,于1991年在湖南衡陽氮肥廠的40kt/a裝置上投產(chǎn),達(dá)到了預(yù)期的效果。
技術(shù)發(fā)展的第二階段——確定了可調(diào)氨醇比的思維模式及工藝條件。當(dāng)流程打通后,氣體的成分控制、新鮮氣的消耗、副產(chǎn)甲醇的量及工藝長久穩(wěn)定運行的條件等均需要摸索,要求有切實可行的工藝方法及操作工藝指標(biāo)。特別是當(dāng)甲醇市場波動時,氨和副產(chǎn)甲醇的產(chǎn)量配合要自如,且經(jīng)濟(jì)性能要好、工藝指標(biāo)也要先進(jìn)。為此我們摸索出了一種可調(diào)氨醇比的工藝條件和設(shè)備配置方法,達(dá)到了醇氨比可在1∶20到1∶1的范圍內(nèi)進(jìn)行調(diào)整,且可保證工藝運行穩(wěn)定,凈化精制氣凈化指標(biāo)不變的目標(biāo)。這種工藝方法的更新,使很多廠家獲得了十分優(yōu)厚的效益回報。
技術(shù)發(fā)展的第三階段——開發(fā)了醇烴化凈化精制工藝,代替甲醇甲烷化(雙甲)工藝。眾所周知,甲烷化反應(yīng)主要是將醇后氣中少量的CO和CO2與氣體中的H2進(jìn)行合成反應(yīng),生成CH4和水,而在氨合成工段CH4為無用的惰性氣體,將要在生產(chǎn)過程中放空掉。因此,我們要求醇后氣中CO和CO2盡量低,另外找出一種能使合成后的CH4量生成少的催化劑來替代純甲烷化的工藝,我們開發(fā)了一種價廉的催化劑,稱之為醇烴化催化劑,以此來取代甲烷化催化劑。首次使用是在湖南衡陽氮肥廠和湖南岳陽化工股份有限公司,達(dá)到了降低新鮮氣消耗約30%的效果。換言之,利用這種催化劑可將原來采用氣態(tài)的廢氣輸出方式換成液態(tài),且此物質(zhì)可回收利用,既降低了有效氣體的消耗,又使工藝操作和流程更加簡化。
基于此,我們成功地將雙甲工藝升級為更加先進(jìn)、更加節(jié)能的醇烴化工藝,此技術(shù)一問世,得到了同行的一致認(rèn)同,成功地獲得了國家科技進(jìn)步二等獎。
不論是雙甲工藝還是醇烴化工藝凈化精制原料氣都比目前很多廠家在用傳統(tǒng)的銅洗法和深度低變—甲烷化法凈化精制工藝有著比較明顯優(yōu)點。
2 醇烴化工藝技術(shù)方案
2.1 化學(xué)反應(yīng)
2.1.1 甲醇化反應(yīng)
原料氣中CO、CO2與H2在一定溫度、催化劑作用下生成粗甲醇,經(jīng)過冷卻、分離送入中間貯糟,此工藝類似于合成氨的聯(lián)醇工藝,但對醇后氣的指標(biāo)要求高,因而要求醇塔要有更高的轉(zhuǎn)化率和更好的熱利用率。
本工序主要反應(yīng)方程式如下
主反應(yīng)
CO+2H2 = CH3OH +102.5kJ/mol
CO2+3H2 = CH3OH+H2O+59.6kJ/mol
副反應(yīng)
4CO+8H2 = C4H9OH+3H2O +49.62kJ/mol
2CO+4H2 = (CH3)2O+H2O+200.2kJ/mol
2CH3OH = (CH3)2O+H2O
CO+3H2 = CH4+H2O +115.6kJ/mol
CO2+H2=CO+H2O-42.9kJ/mol
nCO+2nH2=(CH2)n+nH2O+Q
2.1.2 甲烷化反應(yīng)
經(jīng)甲醇化工序后的醇后氣,含CO+CO2為0.03%~0.3%,經(jīng)換熱后溫度達(dá)到280℃,進(jìn)入甲烷化工序,凈化氣中CO、CO2在催化劑作用下,與H2生成甲烷。反應(yīng)方程如下:
主反應(yīng):
CO +3H2 = CH4 + H2O +206.3kJ/mol
CO2 + 4H2 = CH4 + 2H2O +165.1kJ/mol
副反應(yīng):
O2+2H2=2H2O+C +484.0kJ/mol
2CO=CO2+C+172.5kJ/mol
CO+H2=H2O+C+131.5kJ/mol
Ni+4CO=Ni(CO)4(氣)
2.2 雙甲工藝流程簡圖及說明
2.2.1 雙甲工藝的原則流程
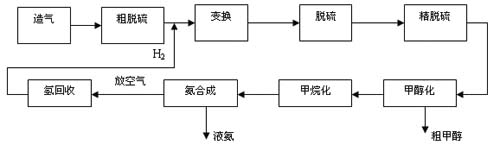
圖1 雙甲工藝的原則流程圖
造氣出來的半水煤氣經(jīng)氣柜后,進(jìn)行粗脫硫,使H2S含量<0.07g/m3,加壓至0.8MPa,進(jìn)入中變;中變出來的氣體CO含量控制在1.5%~5%,經(jīng)脫碳,使CO2下降到0.2%~0.5%,再用無硫氨水進(jìn)行第二次脫硫,將H2S脫除到100×10-6以下;再進(jìn)行精脫硫,使氣體之總硫降到0.1×10-6;氣體再入高壓機(jī)壓縮到3.0~13MPa(壓力的配置與甲醇的產(chǎn)量大小有關(guān),原則上醇產(chǎn)量高時取較低的壓力,反之可取高一點)與醇后氣進(jìn)行換熱,溫度為200℃,進(jìn)入甲醇化反應(yīng)。從甲醇化塔出來的氣體,與新來的氣體換熱,再水冷至40℃左右,進(jìn)入醇分,經(jīng)醇分后CO+CO2達(dá)到0.03%~0.3%;去高壓機(jī)加壓至與氨合成相等壓力,進(jìn)入甲烷化系統(tǒng)(或醇烴化系統(tǒng)),反應(yīng)后的氣體CO+CO2≤10×10-6,經(jīng)換熱冷卻分離水分后,送往合成系統(tǒng)。從合成氨系統(tǒng)排出的吹除氣及液氨貯罐排出的弛放氣,經(jīng)脫氨后去氫回收裝置,利用真空纖維或變壓吸附法對氣體介質(zhì)的選擇吸附,吸附弛放氣中的H2。H2解吸后,回到系統(tǒng)中,未吸附的氣體則排空。
2.2.2 可控制醇氨比的聯(lián)產(chǎn)甲醇雙甲工藝流程(圖2)
雙甲工藝的目的是以凈化精制原料氣為主,副產(chǎn)甲醇為輔。但隨著市場的變化,產(chǎn)品需求也有變化,即有時醇氨比要大幅度調(diào)節(jié)。在甲醇市場好時,醇氨比要求達(dá)到1∶3或更高。此時產(chǎn)醇和精制原料氣都是雙甲(或醇烴化)工藝的重要任務(wù)。這種條件下我們的流程安排原則上是設(shè)置兩個甲醇塔,第一個甲醇塔以產(chǎn)醇(盡量放在低壓級)為主,第二個醇化塔的目的是凈化或深度凈化合成氨原料氣。經(jīng)過第二個塔后CO+CO2含量≤0.3%(這種指標(biāo)既使新鮮氣的消耗不多、又可使熱的利用率高、操作方便簡捷,后面將專門論述)。
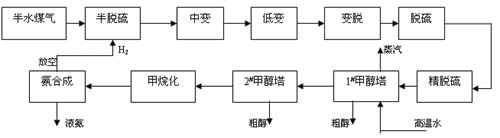
圖2 可調(diào)氨醇比的雙甲流程(醇產(chǎn)量較大)
這種安排很靈活,當(dāng)產(chǎn)甲醇為主,醇氨比很大時,原料氣通過兩塔,在第一塔中CO與CO2的70%轉(zhuǎn)化為醇;第二塔只把剩余30%的CO與CO2 進(jìn)行轉(zhuǎn)化,達(dá)到既產(chǎn)醇又深度凈化的效果,使出醇化系統(tǒng)的CO+CO2總量≤0.3%。如果甲醇市場需求疲軟,工藝以凈化精制為主,甲醇是副產(chǎn)品,并使產(chǎn)量盡量少;例如醇氨比達(dá)1∶10到1∶20,此時可只用一個醇化塔,這一套醇化系統(tǒng)在運行中可以不啟用循環(huán)機(jī);以第二醇化塔作為備用塔;當(dāng)?shù)谝凰呋瘎┗钚韵陆怠⒋呋瘎├匣,再啟用第二塔,同樣全過程均可十分方便地控制入甲烷化爐的CO+CO2含量≤0.3%。
第一級甲醇化采用3.0MPa或8.0MPa,第二級甲醇化及甲烷化與氨合成采用12~32MPa壓力均可(因地制宜視具體情況確定配置方式)。第一級仍以產(chǎn)醇為主,即90%的CO與CO2在此壓力下轉(zhuǎn)化為粗甲醇,剩余10%的CO與CO2在12~32MPa(或30MPa)壓力下轉(zhuǎn)化為甲醇,使CO+CO2含量≤0.3%進(jìn)入甲烷化,甲烷化后氣體中CO+CO2≤10×10-6,送入氨合成。
此流程的優(yōu)點之一是在低壓下合成甲醇,即有占整個原料氣6%~10%的氣體(CO、CO2和生成甲醇需要的H2),不需加壓到更高壓力,大大節(jié)約了電耗。優(yōu)點之二是在3~8MPa壓力下甲醇化,可以利用甲醇化反應(yīng)熱副產(chǎn)中壓蒸汽,作動力用,背壓后蒸汽仍可作為工藝用汽。優(yōu)點之三由于甲烷化(或醇烴化)與氨合成等壓,可免除工藝氣體再過壓縮機(jī)升壓而污染氣體這一環(huán)節(jié),可以較方便地利用氨合成反應(yīng)熱,維持低成分下(CO+CO2≤0.3%)甲烷化爐(或醇烴化爐)的反應(yīng)溫度,而不必開電爐來維持反應(yīng)。
對老廠采用醇烴化工藝,高壓機(jī)沒有3~5MPa這一段,而只有7.8MPa、12.5MPa和30MPa等壓力段,則分別可以在7.8MPa和12.5MPa壓力下進(jìn)行甲醇化,然后升壓至15MPa或32MPa進(jìn)行甲烷化或醇烴化和氨合成。這種流程的節(jié)能效果也很顯著。這種多級不等壓的雙甲工藝是我公司因地制宜既有利于生產(chǎn),又有利于凈化和節(jié)能的通用設(shè)計方法,均有成功的應(yīng)用實例。
2.2.3 聯(lián)產(chǎn)甲醇的醇烴化精制流程
將甲烷化鎳基催化劑改成我公司開發(fā)的醇烴化催化劑,則形成可調(diào)氨醇比的醇烴化精制流程(圖3)。
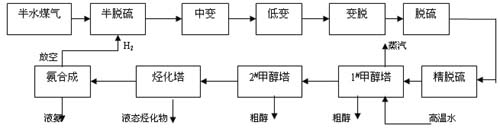
圖3 可調(diào)氨醇比的醇烴化原則流程
取代雙甲工藝的的醇烴化工藝中烴反應(yīng)有如下幾個主要的反應(yīng)式
(2n+1)H2 + nCO →CnH(2n+2) + nH2O (1)
2nH2 + nCO →CnH2n + nH2O (2)
2nH2 + nCO →CnH(2n + 2)O + (n-1)H2O (3)
(3n+1)H2 + nCO2 →CnH(2n+2) + 2nH2O (4)
從反應(yīng)式可看出,醇后氣中CO與CO2在醇烴化催化劑選擇作用下,大部分可以生成醇類、多元醇類及非常少量的CH4。多元醇類物質(zhì)、醇烴類等物質(zhì)均可在常溫下冷凝為液體,有很好的分離性能,環(huán)保性能也很好。這種物質(zhì)可作為燃料使用或作為產(chǎn)品來提純(將其直接送到甲醇精餾崗位提走其中35%的甲醇產(chǎn)品,其余可作為甲醇精餾殘液進(jìn)入燃燒爐內(nèi)燒之)。無疑,由于醇后氣中CO、CO2生成甲烷的量大大減少,送入氨合成后,因甲烷積聚造成的放空量也將減少,由于反應(yīng)物中生成了高碳的產(chǎn)品,大大減少了原料氣的H2消耗,這就是醇烴化工藝的原料氣消耗為什么能大幅度下降的基本原理。
3 雙甲工藝的控制指標(biāo)
3.1 原料氣中二氧化碳含量的控制
原料氣精脫硫后,即進(jìn)入甲醇化系統(tǒng)。要保證原料氣中CO2≤0.2%。CO2過高,甲醇化過程中,生成水多,消耗氫多,增加了副產(chǎn)醇的成本。某廠原料氣中CO2達(dá)0.8%~1.0%,粗甲醇中水含量達(dá)20%以上,并且吸熱量也大,當(dāng)?shù)诙蓟M(jìn)口氣體中CO+CO2量少時,不利于醇化塔內(nèi)的自熱平衡。實際生產(chǎn)還發(fā)現(xiàn)CO2的轉(zhuǎn)化率比CO低得多,原料氣中CO2過高會使醇后氣中CO2高,進(jìn)入甲烷化后,因為1個CO2分子,要耗4個氫分子才能生成1個CH4, 2個H2O分子,因此, CO2多勢必消耗氫更多。
3.2 原料氣中的一氧化碳含量與醇氨比
原料氣中一氧化碳由醇氨比決定,實際生產(chǎn)中我們多以變換爐出口的CO含量來控制醇產(chǎn)量的大小,醇產(chǎn)量高,則醇氨比大,要求原料氣CO含量高,反之,則可低些。
醇氨比依市場情況而定,當(dāng)市場對醇需求量大,應(yīng)適當(dāng)提高醇氨比,然而在一定的工藝流程與系統(tǒng)配置下,醇氨比的提高將會受一定的限制。如表1。
表1 不同醇氨比的氣體成分要求表
醇∶氨
(摩爾比) |
半水煤氣N2含量/% |
變換氣CO含量/% |
進(jìn)甲醇化CO含量/% |
噸合成氨脫碳量/m3 |
1∶15 |
22.5 |
1.28 |
1.69 |
1266.10 |
1∶10 |
21.02 |
1.8 |
2.37 |
1294.83 |
1∶6 |
20.67 |
2.76 |
3.65 |
1352.96 |
1∶4 |
19.35 |
3.85 |
5.09 |
1425.41 |
1∶3 |
18.2 |
4.83 |
6.37 |
1647.73 |
1∶2 |
16.26 |
6.52 |
8.58 |
1642.62 |
1∶1 |
12.34 |
10.11 |
13.25 |
2076.92 |
從表1看出,副產(chǎn)甲醇越多,要求半水煤氣中N2含量越少,即在造氣工段減少加氮空氣;副產(chǎn)甲醇越多,噸氨脫CO2量越大,即對碳銨流程或純堿流程,還需采用其他方法脫除CO2;變換氣中CO含量越高,變換負(fù)荷減輕,加入蒸汽量減少,節(jié)約蒸汽越多。在甲醇市場需求較大、價格較高的情況下,多產(chǎn)甲醇是有利的,但必須有大的造氣能力配套,也要有大的脫碳能力。醇氨比超過1∶6,此時甲醇化必須采用雙級反應(yīng),第一級以產(chǎn)醇為主,第二級以凈化為主。半水煤氣中N2含量降到12.28%以下,就要適當(dāng)增加造氣能力,碳銨流程還要增加脫碳裝置,以維持氨平衡。
醇烴化工藝作為一種合成氨原料氣的凈化精制方法,本工藝副產(chǎn)甲醇是甲醇化凈化的一個副產(chǎn)品,大部分業(yè)主都希望盡可能方便地調(diào)節(jié)各部分的產(chǎn)量。我們在設(shè)備及流程的配置中既考慮了氣體的凈化度——在一床催化劑使用周期的任何一個階段均能達(dá)到后續(xù)工序?qū)铣砂痹蠚鈨艋鹊墓に囈螅挚紤]了在未來甲醇市場較好的情況,需要時,可方便地多產(chǎn)甲醇的要求。因而流程中設(shè)置了兩種不同型式的醇化塔內(nèi)件和“可串聯(lián)也可并聯(lián)”的甲醇化流程,采用了安淳公司的另一項專利技術(shù)——可調(diào)氨醇比的工藝技術(shù)。
生產(chǎn)實踐證明醇氨比控制1∶9左右,控制難度不大,不必增加其他各工段能力,變換氣中CO不是太低,消耗蒸汽不多,雙甲工藝或醇烴化工藝各反應(yīng)塔可不開循環(huán)機(jī),直接通過,大大地節(jié)約了運行電耗。因而從經(jīng)濟(jì)角度考慮是比較合理的。
3.3 醇后氣一氧化碳與二氧化碳的控制
雙甲工藝中,醇后氣尚有少量CO與CO2,在甲烷化中,這些CO、CO2與氫反應(yīng)生成甲烷,送入氨合成系統(tǒng),用放空的方法,使甲烷保持進(jìn)出平衡,不致積累。因為醇后氣中CO2的含量基本上穩(wěn)定,相對來說CO變化波動較大,所以只討論CO的含量與氫消耗及放空量的關(guān)系。見表2。
表2 醇后氣成分與氣體消耗的關(guān)系
醇后氣CO含量/% |
烷后氣CH4含量/% |
噸氨放空氣量/m3 |
噸氨生成CH4耗氫/m3 |
噸氨新鮮氣耗量/m3 |
新鮮氣增加量 | |
凈值量/m3 |
增加/% | |||||
0.591 |
1.65 |
163.44 |
35.04 |
2969.03 |
110.18 |
3.85 |
0.475 |
1.55 |
177.61 |
27.71 |
2946.29 |
57.42 |
3.05 |
0.357 |
1.45 |
162.20 |
20.75 |
2923.10 |
64.23 |
2.2 |
0.239 |
1.35 |
149.59 |
13.75 |
2901.88 |
43.01 |
1.5 |
0.120 |
1.24 |
137.39 |
6.83 |
2880.21 |
21.34 |
0.7 |
0.000 |
1.11 |
116.39 |
0.00 |
2858.87 |
0 |
0 |
注:醇后氣中CH4含量為1.099%。
從表2可以看出,醇后氣中CO越高,即凈化度越低,甲烷化耗氫越多,氨合成放空量越大,噸氨新鮮氣消耗越多,以醇后氣中CO為0(銅洗流程)為比較基準(zhǔn),醇后氣CO由0增加至0.12%和0.591%,噸氨新鮮氣消耗由2858.87m3增加至2880.21m3和2969.05m3,分別多耗原料氣21.34m3、110.18m3。因此,理論上醇后氣中CO含量應(yīng)越低越好。
但CO過低,又引起兩個問題:第一個問題是CO含量越低,要求CO在甲醇化中轉(zhuǎn)化率越高。如果要求醇后氣CO達(dá)到0.1%~0.2%,而醇氨比要求1∶2~1∶5,則要求CO轉(zhuǎn)化率達(dá)到96.7%~98.5%,如此高的轉(zhuǎn)化率,用一般的方法(如中壓聯(lián)醇或低壓甲醇法)是難以達(dá)到的。我們采用雙級甲醇化法,必要的時候采用雙吸不同壓力的方法,即第一級以產(chǎn)醇為主,在低壓下進(jìn)行,第二級以凈化為主,在中壓或高壓下進(jìn)行。但帶來的第二個問題是CO越低,由于缺少反應(yīng)熱量,第二級甲醇化和甲烷化(可醇烴化爐)的反應(yīng)難以自熱平衡,這里就有一個適度指標(biāo)的問題,我們在運行中要找到一個經(jīng)濟(jì)性能好的指標(biāo)——既氣體消耗低,又運行費用低的運行方式,這也是工藝實際和理論結(jié)合,注重運行效果和綜合經(jīng)濟(jì)效益,實踐第一的觀念。
以裝置經(jīng)濟(jì)效益最大化的觀點來看,我們要求當(dāng)甲醇產(chǎn)品銷售好時,多產(chǎn)甲醇;反之,可多產(chǎn)液氨。因而,流程中配置兩種不同形式的醇化塔內(nèi)件(第一醇化塔注重產(chǎn)醇,第二醇化塔注重凈化),達(dá)到既可能大幅度提高醇產(chǎn)量,又可以最大限度地降低醇產(chǎn)物的生成。這就是安淳公司 “可調(diào)醇氨比的雙甲凈化工藝”的核心內(nèi)容之一。
3.4 原料氣中總硫與氨含量的影響
硫?qū)状蓟图淄榛N化)催化劑都會造成永久性毒害。資料介紹,銅基催化劑總硫含量積附達(dá)2%即失活,因此要求原料氣中總硫要控制在0.1×10-6以下,而且要特別注重有機(jī)硫(COS類物質(zhì))的去除。
氨對甲醇化催化劑也與硫一樣有毒害作用,對碳銨流程,原料氣中含氨較多,則要求安排脫氨裝置,使原料氣中氨降到0.1×10-6以下。
3.5 甲烷化(醇烴化)的熱平衡問題
CO的甲烷化(烴化)反應(yīng)是放熱反應(yīng)。在絕熱情況下,每反應(yīng)掉0.1%的CO,溫度上升約7℃,如果入反應(yīng)器CO高,反應(yīng)溫升很高,調(diào)節(jié)不當(dāng),可能燒壞催化劑。醇烴化反應(yīng)和甲烷化反應(yīng)機(jī)理基本一樣,但醇烴化催化劑的反應(yīng)溫度比甲烷化催化劑的溫度低,醇烴化催化劑的溫區(qū)也比甲烷化催化劑溫區(qū)寬,但過高溫度也會使副反應(yīng)增加,不利于生產(chǎn)。因此也必須注意熱的移出和熱平衡。
如前所述,CO過高,噸氨新鮮氣消耗增加,目前公認(rèn)的工藝指標(biāo)CO+CO2一般不能超過0.7%。然而CO+CO2過低,放熱太少,除去了熱損失之后,溫升很少,甚至不能維持反應(yīng)溫度。雙甲(醇烴化)工藝的原則是設(shè)置合理的熱回收裝置,搞好系統(tǒng)的保溫,保證系統(tǒng)滿負(fù)荷運行,在能維持系統(tǒng)熱平衡或較方便地提供外供熱源的前提下,盡量降低醇后氣中CO+CO2含量,以保持反應(yīng)正常進(jìn)行。
3.6 醇產(chǎn)量、氣體成分控制、熱平衡綜合分析
雙甲(醇烴化)工藝的實質(zhì)是將原料氣中的CO+CO2這種后續(xù)氨合成工序稱之為“毒物”的氣體進(jìn)行處理。將此與工藝氣體中的H2進(jìn)行反應(yīng)生成有用的甲醇產(chǎn)品,未反應(yīng)完的CO+CO2再與H2反應(yīng)生成CH4或其他多元醇化物,達(dá)到凈化精制合成氨原料氣之目的。換言之,醇烴化以液態(tài)輸出物的方式,而甲烷化輸出氣態(tài)甲烷。
工藝流程中的第一甲醇化塔可稱為產(chǎn)醇塔,它的主要功能為初步進(jìn)行CO+CO2的去除工作,受轉(zhuǎn)化率的控制,當(dāng)產(chǎn)醇量要求較大時,第一級醇化塔如果要將CO+CO2直接轉(zhuǎn)化到進(jìn)烴化系統(tǒng)的要求指標(biāo)(CO+CO2含量0.03%~0.3%)塔內(nèi)要裝較多的催化劑,用較大的循環(huán)量,啟用較多循環(huán)機(jī),這樣開機(jī)的經(jīng)濟(jì)性能十分不好。為此,流程中配置了第二醇化塔,以此級醇化來完成原料氣的進(jìn)一步凈化工作——將原料氣中的CO+CO2通過合成反應(yīng)降到0.03%~0.3%,完成凈化的氣體再進(jìn)入第三級——醇烴化工段。三者有機(jī)地結(jié)合,各工藝指標(biāo)相互影響、相互制約,只有各部分安全運行,指標(biāo)科學(xué)、特別是總體組合后物料消耗要盡量小、節(jié)能效益要盡量高,才能保證工藝的先進(jìn)性。下面對各段的工藝指標(biāo)進(jìn)行討論。
我們通過理論計算和大量用戶的實踐證明,以凈化為目的的醇烴化工藝,只有在不開循環(huán)機(jī),各部分又不用開電爐的條件下,一次性地通過醇烴化工段,這時的綜合經(jīng)濟(jì)效益才是最好的。達(dá)此目的的醇氨比以小于1∶8為佳。我們在配置設(shè)備和確定催化劑量時,主要是以此操作方式為背景而提出的,但進(jìn)第二個甲醇化塔的CO(不含CO2)含量以不低于1.5%為宜,否則,第二甲醇化塔將會出現(xiàn)熱量不平衡,需外供熱的情形。受單程轉(zhuǎn)化率的控制,在不開循環(huán)機(jī)的條件下,這時醇化出口的CO+CO2最低也只有0.15%(第二醇化塔的空速宜小于8000h-1,催化劑活性要好的條件下),如果要降低第二醇化塔出口的CO+CO2,如達(dá)到微量級(0.01%以下),則應(yīng)降低第二級醇化塔進(jìn)口的CO+CO2含量,這樣將會使第二醇化塔的反應(yīng)不能自熱平衡,將要用較多的外供熱。若要求兩級甲醇化出口總的CO+CO2下降到0.02%,或者說第二甲醇化塔的單程轉(zhuǎn)化率高于95%(要很先進(jìn)的內(nèi)件和較多的催化劑量才能達(dá)到此指標(biāo)),此時第二醇化塔出口的CO+CO2要達(dá)到低于0.02%的指標(biāo),這顯然是很難達(dá)到的,也就是說,這樣的指標(biāo)除導(dǎo)致熱不平衡外,也要求第二醇化塔的轉(zhuǎn)化率要很高。第二級塔的熱平衡問題、第一級或第二級醇化塔的循環(huán)量問題、總的經(jīng)濟(jì)性問題都是要考慮的。這樣,為達(dá)到凈化深度較高——第二醇化塔出口的CO+CO2含量為0.02%將會要開較多的循環(huán)機(jī)和投用較多的外供熱(或開用電爐),循環(huán)量越大,需外供的熱量越多,顯然是得不償失的。
同理,甲烷化(醇烴化)部分進(jìn)口氣體中CO+CO2的含量也和第二醇化塔進(jìn)口一樣受自熱平衡的影響,為了使甲烷化(烴化)爐出口氣中副產(chǎn)品盡量少,降低進(jìn)口的CO+CO2為有效的手段,但有一個外供熱適當(dāng)?shù)膯栴}。我們認(rèn)為,適當(dāng)外供一部分熱源,適當(dāng)降低進(jìn)口的CO+CO2的含量(0.03%~0.3%)為工程中較為節(jié)能的措施。其綜合經(jīng)濟(jì)效益也很好,如果進(jìn)口的成分過低,全部需要利用外供熱,幾乎一點都無自產(chǎn)熱,也是不可取的。
綜合上述,第一級醇化塔進(jìn)口的CO+CO2含量受醇氨比的控制,決定是否需要開啟循環(huán)機(jī),但出口的CO含量應(yīng)控制在1.5%左右,以保證第二醇化塔的自熱能平衡,但也應(yīng)保持不用開循環(huán)機(jī)的操作方式,應(yīng)保證醇化出口的CO+CO2含量在0.03%~0.3%。醇烴化在有外供適當(dāng)熱的條件下,可適當(dāng)降低進(jìn)口氣體中的反應(yīng)物濃度,但應(yīng)以總體經(jīng)濟(jì)效益較好為目標(biāo)。
3.7 醇化和甲烷化(烴化)系統(tǒng)壓力的選擇
3.7.1 醇化系統(tǒng)壓力的選擇
選擇醇化系統(tǒng)的操作壓力無疑首先要考慮催化劑的適用壓力,目前甲醇催化劑的操作壓力可在3.0~32MPa壓力范圍內(nèi)。我們的思路是,當(dāng)需要醇產(chǎn)量較大時,盡量將醇化系統(tǒng)的壓力放置在低一點的壓力級上,這樣有兩點好處:一是可以減少制醇時氣體的壓縮功耗,二可以提高醇產(chǎn)品的質(zhì)量。但從反應(yīng)機(jī)理來看,醇化系統(tǒng)壓力過高,將會使副反應(yīng)增加,不利于醇產(chǎn)品的質(zhì)量提高和醇產(chǎn)品精餾系統(tǒng)能耗降低。
當(dāng)醇氨比較高,流程采用二級醇化方案時,就有第一級和第二級甲醇壓力的選擇問題。我們考慮是為了使二級醇化塔可以串聯(lián)使用(兩個塔可以互換,固定床反應(yīng)器的醇化塔),只有壓力在一個級別才好控制和互換;诖耍b置壓力均設(shè)置在同一級壓力。但如果是廠家原舊聯(lián)醇設(shè)備或有氨合成設(shè)備改造成甲醇化設(shè)備,又有能力限制等問題,我們才將兩級醇不設(shè)在一個壓力級別。當(dāng)?shù)谝患壌蓟膲毫^低(3.0~8.0MPa)時,如果第二級醇化為與第一個等壓的醇化塔,也不利于轉(zhuǎn)化率的提高,必須采用“雙級雙壓制”——可專設(shè)一個處理大氣量的醇塔在盡量低的壓力級工作,凈化用的醇塔可在13~32MPa壓力級內(nèi)。
3.7.2 甲烷化(醇烴化)系統(tǒng)壓力級的選擇問題
傳統(tǒng)的甲烷化爐操作壓力為2.0~3.0MPa,由于受流程和甲醇催化劑的限制,此工藝將甲烷化爐提到了高壓下運行(13~32MPa)。在這種工藝中,我們選擇此壓力級的思路是:盡量將甲烷化的壓力選擇在靠第二級醇化塔的壓力級。這樣有兩種好處,一個好處是醇化后的氣體不需再用壓縮機(jī)來提壓,減少了由于壓縮機(jī)壓縮后,氣體中的油含量增加對甲烷化(醇烴化)催化劑的污染;第二個好處是,兩工序放在相同壓力級,可以和醇化系統(tǒng)共用循環(huán)機(jī)(循環(huán)機(jī)用于甲烷化催化劑或烴化催化劑的升溫還原及降溫)。
但如果是合成設(shè)備改造成的甲烷化或醇烴化系統(tǒng),且塔的能力相對較小,可將甲烷化或醇烴化放置在最高壓力級(與合成系統(tǒng)等壓),這樣的好處有:可少裝一些催化劑,提高一點運行空速,另外可獲得較高的轉(zhuǎn)化率,減少熱的損失。但這樣也會使合成工段的運行壓力下降。
綜合言之,工藝的配置及壓力的選擇,應(yīng)根據(jù)不同廠家的具體條件、甲醇產(chǎn)量的大小、不同廠家的利舊設(shè)備情況,按照上述討論的條件,因地制宜地選擇各級壓力,不可一成不變。
4 甲醇化反應(yīng)器
我國的現(xiàn)有甲醇塔大致有三類:一是單管折流式反應(yīng)器,二是多段軸徑向降溫方式的反應(yīng)器,三是低壓管殼式等溫反應(yīng)器。
單管折流式反應(yīng)器已多年運行于合成氨廠的聯(lián)醇裝置,內(nèi)件是在單管折流式氨合成塔基礎(chǔ)上衍生出來的,其結(jié)構(gòu)特點是:冷管長,換熱面積大,下部換熱器面積也較大,運行時軸向溫差較小,零米溫度較高,運行平穩(wěn);缺點是阻力較大,同平面溫差較大,循環(huán)量也較大,催化劑使用周期較短。
低壓管殼式反應(yīng)器的結(jié)構(gòu)特點:壓力為5~8MPa,直徑為φ2000~φ4200mm,內(nèi)裝有φ38×2mm或φ48.3×2mm的雙相鋼材料的催化劑管,面積1302~2381m2,管內(nèi)裝催化劑,管外產(chǎn)2.7~3.9MPa飽和蒸汽,用于單醇裝置。黑龍江化工總廠引進(jìn)的雙甲聯(lián)醇裝置,一級甲醇塔采用這種反應(yīng)器。其優(yōu)點是管內(nèi)完全是等溫反應(yīng),用蒸汽壓力調(diào)節(jié)溫度,升溫還原容易,操作平穩(wěn),操作壓力低,壓縮氣體功耗少,并能副產(chǎn)2.7~3.9MPa飽和蒸汽(噸醇約產(chǎn)1t蒸汽),缺點是設(shè)備造價較高,裝填催化劑較困難。
多段軸徑向反應(yīng)器,其結(jié)構(gòu)特點為:(1)4~5個反應(yīng)段,其中有一段為內(nèi)冷式換熱,其他均為冷激絕熱式;(2)設(shè)置塔外換熱器,塔內(nèi)沒有換熱器或換熱面積很;(3)設(shè)置前置式或后置式蒸汽熱回收器;(4)三個段為徑向段;(5)自卸催化劑。多段軸徑向反應(yīng)器的優(yōu)點是:(1)各段絕熱溫升控制5℃左右,基本上沿著最適溫度曲線進(jìn)行反應(yīng),同平面溫差在3℃以內(nèi);(2)循環(huán)量較小,阻力小,為0.3~0.4MPa;(3)操作彈性好,適用于不同的醇氨比;(4)結(jié)構(gòu)比較簡單,適用于高、中壓大直徑(φ1200mm以上)聯(lián)醇塔使用;(5)裝卸催化劑容易。
我公司設(shè)計的醇化反應(yīng)器對不同的醇氨比其內(nèi)件結(jié)構(gòu)不一樣:產(chǎn)醇量大的內(nèi)件和以凈化為目的的內(nèi)件設(shè)計方式是不一樣的,前者盡量提高反應(yīng)效率,減少循環(huán)機(jī)的開啟量。后者較多地注意提高轉(zhuǎn)化率和充分利用熱能。
總的來說,對甲醇化塔的設(shè)計我公司注重降低塔的阻力。因為,采用此種凈化方法,工藝氣體要經(jīng)過二到三個催化劑床,每床層都存在阻力降,如果不盡量降低阻力,則會增加壓縮機(jī)的電耗,對節(jié)能不利。我們的控制指標(biāo)是醇烴化系統(tǒng)和雙甲系統(tǒng)兩個部分總的阻力降應(yīng)不能超過1.5MPa。
5 雙甲工藝與深度低變—甲烷化的比較
合成氨原料氣的凈化精制方法中,有一種比銅洗先進(jìn),使用也有很長歷史的深度低變—甲烷化法。其主要特點是要求低變氣中CO為0.3%, 進(jìn)甲烷化CO與CO2為0.7%。按此指標(biāo)大多數(shù)流程和操作存在一些問題。
變換氣中CO降到0.3%,按變換反應(yīng)平衡理論,要求大量的過量蒸汽進(jìn)入變換爐,即汽氣比很大。如果以天然氣、油為原料的轉(zhuǎn)化法制取原料氣,或以煤為原料的德士古水煤漿加壓氣化法制取水煤氣,由這些方法制取的原料氣含有大量的飽和蒸汽,其中的CO經(jīng)中變直接串低變,即可降到0.3%以下。圖4是魯南第二化肥廠德士古水煤漿加壓氣化制取的煤氣凈化精制方法,方法雖然簡單,但德士古法基建投資很大,國內(nèi)許多化肥廠無法采用。
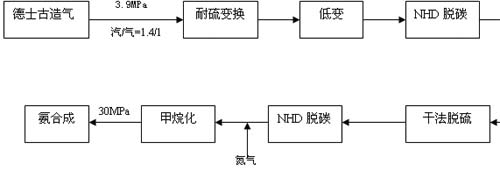
圖4 德士古加壓氣化、深度低變—甲烷化流程
如果以煤為原料,采用空氣—蒸汽間歇法制半水煤氣,因進(jìn)入變換系統(tǒng)的半水煤氣水蒸氣含量很少,要將半水煤氣中的CO降至0.3%以下。為了有利于變換平衡,反應(yīng)到一定程度后,必須將生成的二氧化碳脫除,這就要求兩次變換,兩次脫碳,反復(fù)升溫、降溫。
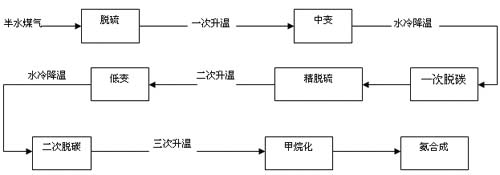
圖5 魯南第一化肥廠的中低變─甲烷化流程方框圖
由圖看出流程太復(fù)雜,設(shè)備臺數(shù)很多,且反應(yīng)熱利用率太低(兩次變換之后,都要用水降溫)。為了簡化流程,某小氮肥廠采用了中、耐硫低變—甲烷化流程。如圖6。
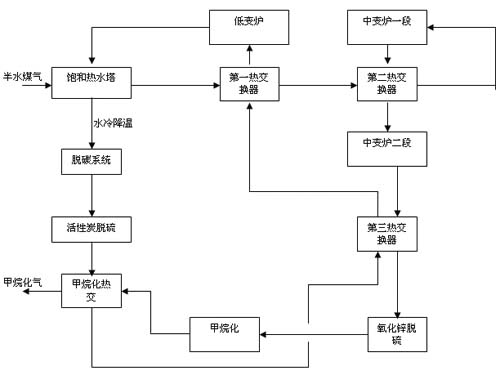
圖6 中變、耐硫深度低變——甲烷化流程
0.8~1.2MPa的半水煤氣經(jīng)過飽和熱水塔,第一熱交,被中變二段來的熱氣加熱,進(jìn)入第二熱交,被中變一段來的熱氣繼續(xù)加熱,進(jìn)入中變一段反應(yīng),一段反應(yīng)熱氣經(jīng)第二熱交冷卻進(jìn)入中變二段反應(yīng),反應(yīng)熱氣經(jīng)第三熱交和第一熱氣進(jìn)入熱水塔降溫,水冷、脫碳、精脫硫,進(jìn)入甲烷化熱交,被甲烷化熱交加熱,再進(jìn)入第三熱交,被中變一段氣加熱至250~280℃,進(jìn)入甲烷化爐反應(yīng),反應(yīng)后甲烷化熱氣經(jīng)甲烷化熱交冷卻,再水冷、分離、加壓送至氨合成系統(tǒng)。
此法中變后不經(jīng)脫碳就進(jìn)入低變,流程并不復(fù)雜,但采用該法物耗(原料氣與蒸汽耗)很高。表3是不經(jīng)脫碳即深度低變—甲烷化的物料平衡表,表4是中低變—雙甲工藝物料平衡表,我們可利用這兩個表來分析說明消耗高的具體情況。
表3 深度低變—甲烷化物料表
組分 |
變換氣 |
原料氣 |
甲烷氣 | |||
量/m3 |
比例/% |
量/m3 |
比例/% |
量/m3 |
比例/% | |
H2 |
2278.64 |
52.00 |
2278.64 |
74.36 |
2214.61 |
73.81 |
N2 |
739.42 |
16.84 |
739.42 |
24.13 |
739.42 |
24.64 |
CO |
13.17 |
0.3 |
13.17 |
0.55 |
|
|
CO2 |
1332.12 |
30.34 |
6.13 |
0.2 |
|
|
CH4 |
10.11 |
0.23 |
10.11 |
0.33 |
29.41 |
0.98 |
Ar |
16.85 |
0.38 |
16.85 |
0.43 |
16.85 |
0.57 |
合計 |
4390 |
100 |
3064.32 |
100 |
3000.29 |
100 |
表4 中變串低變—雙甲工藝物料表
組分 |
半水煤氣 |
變換氣 |
原料氣 |
醇后氣 |
烴后氣 | |||||
量/m3 |
比例/% |
量/m3 |
比例/% |
量/m3 |
比例/% |
量/m3 |
比例/% |
量/m3 |
比例/% | |
H2 |
1407.82 |
40.02 |
2388.74 |
53.12 |
2317.43 |
73.55 |
2162.78 |
74.08 |
2133.59 |
73.83 |
N2 |
741.00 |
21.06 |
741.00 |
16.48 |
723.18 |
22.95 |
722082 |
24.76 |
722.82 |
25.01 |
CO |
1063.79 |
30.24 |
82.94 |
1.84 |
81.03 |
2.57 |
5.84 |
0.20 |
|
|
CO2 |
278.78 |
7.92 |
1259.64 |
28 |
51.68 |
0.16 |
29.19 |
0.10 |
|
|
CH4 |
20.88 |
0.59 |
20.88 |
0.46 |
18.64 |
0.59 |
19.27 |
0.66 |
28.03 |
0.97 |
Ar |
5.51 |
0.16 |
5.51 |
0.12 |
5.51 |
0.17 |
5.51 |
0.19 |
5.51 |
0.19 |
合計 |
3517.85 |
100 |
4496.47 |
100 |
3150.94 |
100 |
2919.43 |
100 |
2889.94 |
100 |
通過對表3、4的分析計算,有下述結(jié)論。
(1)雙甲工藝噸氨耗精煉氣比深度低變—甲烷化耗精煉氣少, 前者2889.94m3,后者為3000.29m3,相差110.35m3。即雙甲工藝噸氨少耗精煉氣3.82%。
(2)雙甲工藝?yán)迷蠚庵械囊谎趸己投趸几碑a(chǎn)甲醇(醇氨比1:10),即噸氨副產(chǎn)醇100kg,沒有副產(chǎn)品。
(3)深度低變)—甲烷化工藝要求變換氣中一氧化碳小于或等于0.3%,如果中變氣不經(jīng)脫碳,即進(jìn)入深度低變,查變換反應(yīng)平衡數(shù)據(jù),只有汽/氣R=0.6,溫度t=180℃下,出口氣中一氧化碳才小于或等于0.3%。按此計算,噸氨入爐蒸汽需1632.10kg。
(4)如采用中低變—烴化工藝,低變出口氣中一氧化碳為1.84%,溫度210℃(考慮平衡溫距20℃)汽/氣R=0.35,則噸氨需要入爐蒸汽989.29kg。
(5)如果兩者都設(shè)有飽和熱水塔回收蒸汽,回收效率一樣,則雙甲工藝比深度低變—甲烷化變換時噸氨少耗蒸汽642.81kg。
綜上所述,中低變—雙甲工藝與深度低變—甲烷化比較,雙甲工藝適應(yīng)能力更強(qiáng),應(yīng)用范圍更廣泛,噸氨耗精煉氣少3.82%,變換蒸汽少耗64.97%,且還能副產(chǎn)甲醇10%。
6 雙甲(醇烴化)工藝與傳統(tǒng)聯(lián)醇工藝的比較
6.1 傳統(tǒng)聯(lián)產(chǎn)甲醇存在的問題
(1)當(dāng)醇氨比較大時,甲醇塔得多塔串聯(lián),系統(tǒng)的阻力大,最高時系統(tǒng)阻力達(dá)3.0MPa。
(2)當(dāng)醇氨比較大時,甲醇催化劑的使用壽命較短,一般為3~8個月。
(3)醇氨比較大時,反應(yīng)熱較大,熱沒有回收或回收率不高,循環(huán)機(jī)開啟量也大,造成電耗高和系統(tǒng)阻力大的惡性循環(huán)。
(4)醇后氣中的CO+CO2較高,一般可達(dá)1.5%~2.0%。
(5)醇后氣再進(jìn)一步精制需要銅洗工段、堿洗工段,銅洗和堿洗的操作費用大(噸氨50~90元/t)。
6.2 雙甲(醇烴化)工藝聯(lián)產(chǎn)甲醇的優(yōu)勢
6.2.1 雙甲工藝聯(lián)產(chǎn)甲醇的優(yōu)勢
(1)醇后氣采用甲烷化,砍掉銅洗、堿洗,節(jié)約銅、醋酸、自用氨、加熱銅液熱量、冷凍銅液冷凍量,甲烷化(醇烴化)成本只有催化劑的耗量。
(2)采用雙塔流程和徑向反應(yīng)器,阻力大幅度降低,雙甲總阻力只有1.0~1.5MPa。
(3)以產(chǎn)醇為主的反應(yīng)器副產(chǎn)蒸汽,當(dāng)醇氨比較大時,可減少循環(huán)量或不開循環(huán)機(jī),能耗低。
(4)可多產(chǎn)甲醇,因為醇后氣中CO+CO2由傳統(tǒng)流程的1.5%~2%經(jīng)甲醇化下降至0.1%~0.3%,增加的甲醇產(chǎn)量為氨產(chǎn)量的1/12。
(5)甲醇化和傳統(tǒng)聯(lián)醇投資相當(dāng),甲烷化比銅洗設(shè)備臺數(shù)少,占地面積少,投資要少。甲烷化設(shè)備還可用退役合成設(shè)備,投資更少。
(6)甲醇化反應(yīng)溫和,催化劑使用壽命長。
6.2.2 節(jié)能效益顯著
雙甲(醇烴化)工藝與傳統(tǒng)聯(lián)產(chǎn)甲醇比較,有節(jié)能、節(jié)物、運行穩(wěn)定、凈化環(huán)境的四個明顯優(yōu)點。
表5為醇烴化工藝與銅洗操作費用比較,有一部分尚未計入的計算數(shù)據(jù),可供參考。
表5 醇烴化工藝流程與銅洗流程的費用比較表(噸總氨)
項目名稱 |
單 價
/元 |
銅 洗 |
醇 烴 化 |
備 注 | ||
噸氨消耗 |
運行費/元 |
噸氨消耗 |
運行費/元 | |||
自用氨 |
1.4 |
8.2kg |
11.5 |
0 |
|
|
電解銅 |
22 |
0.12kg |
4.64 |
0 |
|
|
冰醋酸 |
5 |
0.24kg |
1.2 |
0 |
|
|
蒸汽 |
0.045 |
350kg |
15.75 |
0 |
|
|
電 |
0.25 |
120.8kwh |
30.2 |
11.61kwh |
2.90 |
含銅洗和烴化的冰機(jī)電耗 |
冷卻水 |
1.00 |
25t |
25.00 |
21.92t |
21.92 |
|
烴化催化劑 |
22 |
0 |
0.00 |
0.021kg |
0.462 |
|
醇化催化劑 |
32 |
0 |
0.00 |
0.14kg |
4.48 |
|
合 計 |
|
|
86.29 |
|
29.76 |
|
注:計算單價為2000年的單價,現(xiàn)時可根據(jù)具體情況進(jìn)行變更。
由表5可見,雙甲或醇烴化工藝的運行費用將顯著降低。噸氨降低約56.53元,生產(chǎn)10kt氨,將節(jié)約運行費用56.53萬元。
另外銅洗的微量一般都在20×10-6以上,且經(jīng)常帶液噴液,生產(chǎn)運行不穩(wěn)定。雙甲工藝很穩(wěn)定,微量(5~10)×10-6。銅洗操作過程中,跑、冒的銅液污染大氣、河水及生產(chǎn)現(xiàn)場,雙甲工藝沒有液體、氣體的滲漏,環(huán)境良好。
7 醇烴化工藝的重大進(jìn)步
醇烴化工藝是合成氨具有革命性的成果,它可使原料氣CO+CO2降到(5~10)×10-6。醇烴化工藝除了精制氣體功能之外,還利用變換后的CO、脫碳后的CO2副產(chǎn)粗甲醇或醇醚混合物,生產(chǎn)中完全可實現(xiàn)零污染、零排放。
粗甲醇可以用常壓精餾方法得到精甲醇。醇醚混合物中,二甲醚含量達(dá)30%~40%。這種混合物是易燃的優(yōu)質(zhì)燃料,可替代液化氣作民用燃料。也可用加壓精餾方法,得到二甲醚和甲醇。
副產(chǎn)物是粗甲醇還是醇醚混合物,決定于采用何種催化劑。用一般的甲醇催化劑,生產(chǎn)出來副產(chǎn)物是甲醇,采用我公司開發(fā)的XMM催化劑,則生產(chǎn)出來的是醇醚混合物。
雙甲工藝是甲醇化和甲烷化,上述將甲醇化催化劑改為醇醚催化劑,生產(chǎn)醇醚混合物,就稱為甲基化,如果將甲烷化催化劑由鎳基催化劑改為鐵基催化劑,則CO、CO2與氫反應(yīng)生成甲醇、乙醇等多元醇和烷烴化物。
用醇烴化代替甲烷化之后,有四大優(yōu)點:一是醇后氣中CO+CO2含量可以適當(dāng)提高,醇烴化反應(yīng)器,反應(yīng)熱多,完全可自熱平衡;二是進(jìn)入的CO、CO2大部分生成了醇類物和碳?xì)浠衔铮诔叵吕淠秊橐后w,生成的甲烷很少,從而使進(jìn)入氨合成系統(tǒng)的CH4大大減少,即減少了合成放空量,降低噸氨原料氣消耗;三是烴化催化劑的反應(yīng)溫度為220~250℃,比甲烷化催化劑的反應(yīng)溫度280~320℃要低,且醇烴化催化劑的溫區(qū)較寬(220~500℃),有利于提高轉(zhuǎn)化率和利用外供熱;四是甲烷化催化劑當(dāng)醇后氣有甲醇或二甲醚存在時(這種狀況是難免的),甲醇或二甲醚氣體進(jìn)入甲烷化塔內(nèi)將影響甲烷化的反應(yīng)。而醇烴化催化劑則無此現(xiàn)象,醇烴化反應(yīng)有甲醇反應(yīng)在其中,因而甲醇或二甲醚分子在醇烴化催化反應(yīng)器中能順利通過,對反應(yīng)沒有任何影響。
用醇烴化代替甲烷化之后,有四大優(yōu)點:一是醇后氣中CO+CO2含量可以適當(dāng)提高,醇烴化反應(yīng)器,反應(yīng)熱多,完全可自熱平衡;二是進(jìn)入的CO、CO2大部分生成了醇類物和碳?xì)浠衔铮诔叵吕淠秊橐后w,生成的甲烷很少,從而使進(jìn)入氨合成系統(tǒng)的CH4大大減少,即減少了合成放空量,降低噸氨原料氣消耗;三是烴化催化劑的反應(yīng)溫度為220~250℃,比甲烷化催化劑的反應(yīng)溫度280~320℃要低,且醇烴化催化劑的溫區(qū)較寬(220~500℃),有利于提高轉(zhuǎn)化率和利用外供熱;四是甲烷化催化劑當(dāng)醇后氣有甲醇或二甲醚存在時(這種狀況是難免的),甲醇或二甲醚氣體進(jìn)入甲烷化塔內(nèi)將影響甲烷化的反應(yīng)。而醇烴化催化劑則無此現(xiàn)象,醇烴化反應(yīng)有甲醇反應(yīng)在其中,因而甲醇或二甲醚分子在醇烴化催化反應(yīng)器中能順利通過,對反應(yīng)沒有任何影響。
8 應(yīng)用舉例
(1)湖南衡陽市氮肥廠
該廠以煤為原料,主產(chǎn)品為尿素,中低低變換、NHD脫碳,12MPa甲醇化(雙φ800mm反應(yīng)器),先期用甲烷化反應(yīng)器,后改成了30MPa烴化反應(yīng)器,合成氨實際能力80kt/a,副產(chǎn)甲醇8kt/a,1992年7月投產(chǎn),正常運行至現(xiàn)在,投資400萬元(利用舊高壓設(shè)備、舊合成框架)。
(2)湖南郴化集團(tuán)橋口氮肥廠
該廠以煤為原料,主產(chǎn)品為尿素和碳銨,中低低變換,2.8MPa碳丙脫碳,12MPa甲醇化、甲烷化均為φ800mm反應(yīng)器,雙甲與合成氨在同一個框架,設(shè)計為凈化精制80kt/a合成氨原料氣,副產(chǎn)12kt甲醇,F(xiàn)在合成氨實際能力60kt/a,副產(chǎn)甲醇6kt/a,1996年投產(chǎn)至今,正常運行,投資600萬元,全套新設(shè)備。
(3)湖南岳陽化肥廠
該廠以煤為原料,主產(chǎn)品為尿素,中低低變換,2.8MPa下NHD脫碳,12MPa甲醇化(雙φ800mm反應(yīng)器),30MPa烴化反應(yīng)器(φ800mm反應(yīng)器),φ1600mm合成系統(tǒng),實際產(chǎn)量100kt/a合成氨,副產(chǎn)甲醇12kt/a。2000年1月投產(chǎn),投資300萬元(利用原有甲醇系統(tǒng)和退役的φ800mm合成高壓設(shè)備)。
(4)山西豐喜集團(tuán)臨猗化肥廠
該廠以煤為原料,12MPa甲醇化(雙φ1400mm反應(yīng)器),12MPa甲烷化(φ1200mm反應(yīng)器),30MPa氨合成(φ1400mm合成系統(tǒng)),年產(chǎn)120~130kt合成氨,聯(lián)產(chǎn)30~40kt甲醇,雙甲及氨合成為全新設(shè)備,合成、雙甲為一個框架,一個操作室,投資約3000萬元。
(5)河北邯鋼集團(tuán)化肥廠
該廠以煤為原料,雙甲工藝(φ1000mm甲醇化塔兩個,φ1000mm醇烴化塔一個,利用退役氨合成系統(tǒng)設(shè)備),氨合成(φ1600mm系統(tǒng),全新設(shè)備),氨合成、醇化塔、甲烷化塔均為32MPa壓力級。合成雙甲為同一框架,同一操作室,雙甲工藝投資300萬元,氨合成投資2000萬元。
(6)河南心連心化工有限公司
該廠2003年投產(chǎn)一套160kt/a總氨的醇烴化及氨合成工段,醇化為雙級DN1400系統(tǒng),壓力為13MPa,烴化為DN1000系統(tǒng)(利用原DN1000合成系統(tǒng)改造而成)壓力為32MPa,氨合成系統(tǒng)為一套DN1600系統(tǒng),投用后,系統(tǒng)超設(shè)計能力運行,目前每天產(chǎn)醇200t,產(chǎn)氨450t,醇化系統(tǒng)阻力降約0.6MPa,烴化和合成系統(tǒng)運行壓力僅25MPa。新裝置投運后,工廠一天比原來增利20~25萬元,取得了很好的經(jīng)濟(jì)效益。
(7)山西天脊集團(tuán)晉城化工股份有限公司
該廠新建一套220kt/a合成氨裝置,我公司為其提供醇烴化及氨合成聯(lián)合工段的設(shè)計及設(shè)備。于2003年9月全部開車,一次成功。醇化塔為兩級DN2000塔,烴化塔為DN1800塔,氨合成塔為一套DN1400、一套DN1600。醇烴化系統(tǒng)的壓力為13MPa,氨合成系統(tǒng)的壓力為32Ma.。
(8)山西蘭花集團(tuán)化肥分公司
該廠 新擴(kuò)一套120kt/a系統(tǒng),我公司為其作了13MPa壓力的醇烴化工藝。于2003年10月一次開車成功。
目前正在為山東瑞星化工股份有限公司、山東德齊龍化工有限公司、江蘇新沂恒盛化肥有限公司、江蘇華爾潤集團(tuán)股份有限公司、江蘇張家港市華源化工有限公司,山東明水化肥廠、山西天脊集團(tuán)等廠進(jìn)行醇烴化及氨合成工段的設(shè)計。最大合成氨能力為400kt,最小合成氨能力有120kt/a,近期將陸續(xù)投用。
9 結(jié)束語
雙甲工藝及醇烴化工藝均是我國首先提出、首先工業(yè)化成功的一項先進(jìn)技術(shù),它是合成氨生產(chǎn)技術(shù)的一項重大革新。它有兩大功能:一是將合成氣中CO+CO2脫除到(5~10)×10-6以下,二是能聯(lián)產(chǎn)甲醇。在甲醇需求市場旺盛的情況下,可提高一氧化碳含量,多產(chǎn)甲醇,反之可少產(chǎn)甲醇,其醇氨比可在1∶1到1∶20之間調(diào)節(jié)。雙甲(醇烴化)工藝中的甲醇化壓力可在3.0MPa到15.0MPa進(jìn)行,也可用退役高壓容器,按30MPa運行。它與變換—脫碳—銅洗工藝,變換—脫碳—聯(lián)醇—銅洗工藝或深度低變——甲烷化流程相比,流程短、精制度高,操作穩(wěn)定可靠,節(jié)約能耗、物耗,經(jīng)濟(jì)效益顯著,且適用性強(qiáng),既適用于石腦油、天然氣,又適用以煤為原料的工廠,同時產(chǎn)品結(jié)構(gòu)改善,既生產(chǎn)氨,又生產(chǎn)甲醇,如果更換催化劑,還可以生產(chǎn)二甲醚和甲基燃料。利用本工藝改造老廠,可在兩年內(nèi)回收全部投資,如果新建氨廠采用醇烴化工藝更加合理。目前新建的合成氨廠或改造擴(kuò)大能力的廠家,涉及到凈化精制問題時,無一例外都是考慮用雙甲工藝或醇烴化工藝,該技術(shù)已經(jīng)列為化肥廠“污水零排放”的首選技術(shù)。
湖南安淳公司作為技術(shù)和專利持有者,正大面積在全國合成氨行業(yè)推廣。我們將會不斷完善技術(shù),為合成氨行業(yè)的技術(shù)進(jìn)步而努力。

元豐資訊:
氮肥與甲醇技術(shù)網(wǎng)
尿素網(wǎng)
造氣網(wǎng)
二甲醚網(wǎng)
尿素世界網(wǎng) (英文版)
產(chǎn)品技術(shù)庫
VIP商務(wù)俱樂部
化工論壇
QQ群大聯(lián)盟
地址:成都市青白江區(qū)怡湖芳鄰18棟8號 電話:028-83667786,83667576,89309098 傳真:028-83667578